Produkcja cementu, wapna i papieru
Nasza oferta dla branży produkcji cementu, wapna i papieru
Proces kalcynacji węglanów wapnia oraz ich dalsza termiczna przeróbka odgrywa kluczową rolę w wielu branżach, szczególnie w budownictwie i przemyśle chemicznym.
Klinkier cementowy i wapno kalcynowane to podstawowe składniki materiałów budowlanych. Wapno palone znajduje również szerokie zastosowanie w różnych procesach przemysłowych, takich jak produkcja pulpy papierniczej, sody czy cukru. Obecnie produkcja oparta na tych procesach jest pod silną presją efektywności i koniecznością zrównoważonego rozwoju. Emisja dwutlenku węgla pochodzącego z surowców znacząco wpływa na ekonomikę procesu kalcynacji, dlatego kluczowe jest zapewnienie efektywności na każdym etapie. Bezawaryjne kampanie produkcyjne, minimalizacja postojów remontowych oraz efektywna termicznie wykładzina pieca mogą zapewnić istotną przewagę konkurencyjną. Misją PCO jest wspieranie partnerów w zakresie technologii ogniotrwałych dla pieców wapienniczych i cementowniczych – od opracowań inżynierskich, poprzez wspólny dobór optymalnych rozwiązań materiałowych i technologii instalacyjnych, aż po logistykę w dowolne miejsce na świecie oraz montaż i nadzór. Wierzymy, że niezawodna jakość naszych produktów i obsługi, w połączeniu z kompleksowym wsparciem, pozwala minimalizować przestoje produkcyjne i wspiera naszych partnerów w osiąganiu wyższej konkurencyjności oraz realizacji celów zrównoważonego rozwoju.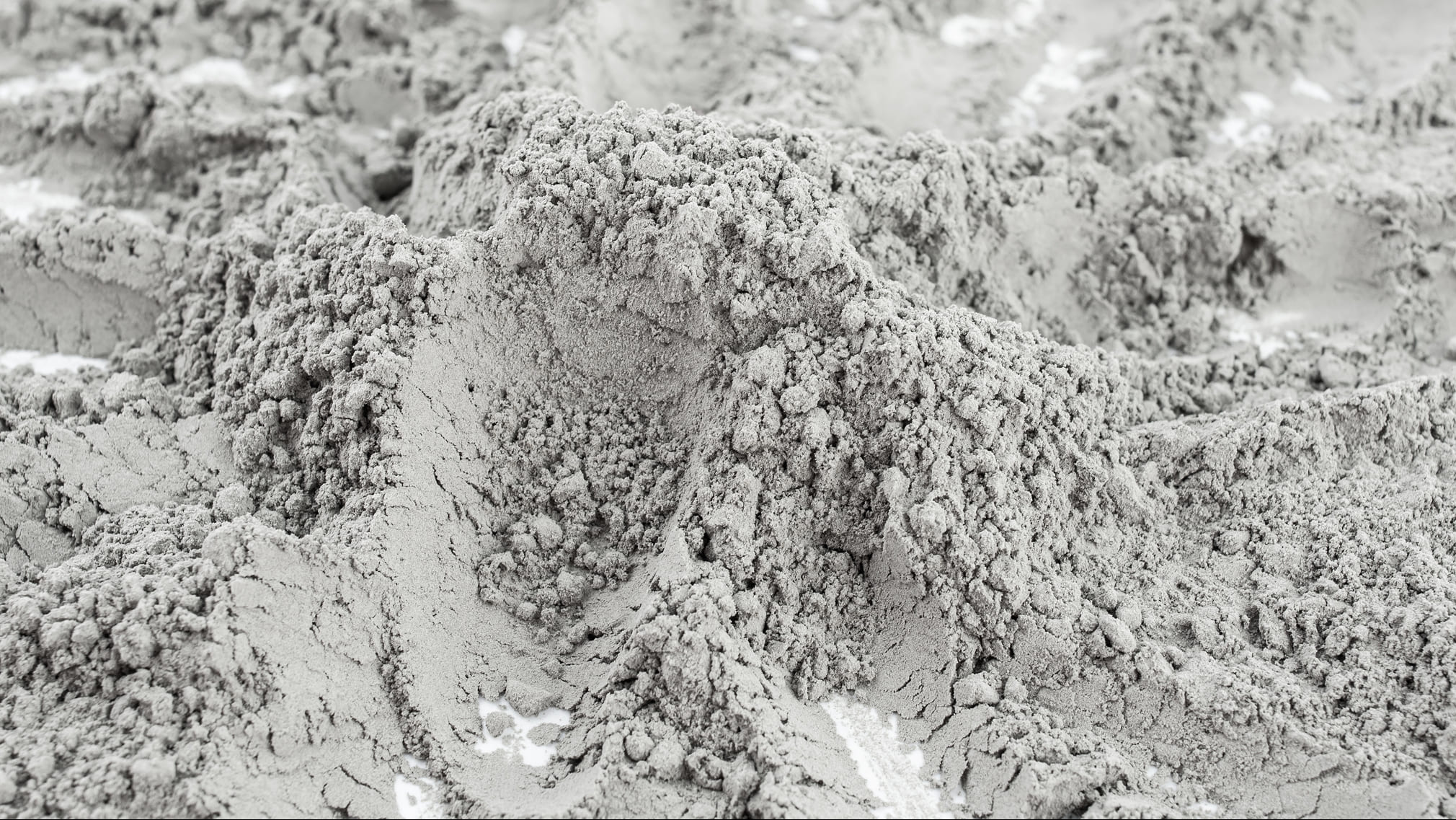
Jak możemy pomóc
Projektujemy
- Dobór odpowiednich gatunków materiałów ogniotrwałych, dostosowanych do warunków prowadzenia procesu produkcji
- Wybór optymalnego układu zabudowy wyłożenia ogniotrwałego, uwzględniającego specyfikę urządzenia, strefy, warunki eksploatacyjne oraz preferencje użytkownika
- Analizy przepływów cieplnych dla różnych wariantów wyłożeń ceramicznych (porównawcze A/B)
- Optymalizację konstrukcji wyłożeń pod kątem wydłużenia trwałości i redukcji strat ciepła
Produkujemy i dostarczamy
- Wyroby szamotowe i wysokoglinowe o podwyższonej odporności na ścieranie, przeznaczone do zabudowy wież wymienników, kanałów trzeciego powietrza, kalcynatorów, duktów, komór wzniosu w instalacjach cementowych oraz chłodniejszych stref wlotowych i wylotowych w piecach wapienniczych
- Innowacyjne betony niskocementowe i bezcementowe do szerokiego zakresu zastosowań w instalacjach cementowych, wzbogacone o dodatki takie jak SiC i ZrO
- Wyroby izolacyjne do warstw ochronnych pieców szybowych i obrotowych, w tym o podwyższonej wytrzymałości mechanicznej
- Wyroby prefabrykowane gotowe do instalacji nie wymagające dotrzymania reżimu wygrzewania
Zabudowujemy
- Demontaż i montaż obmurza we wszystkich urządzeniach instalacji produkcji cementu, a także w piecach szybowych i wieloszybowych
- Odbiór zdemontowanego wyłożenia ceramicznego (ceramicznego złomu piecowego)
- Naprawy bieżące i obsługa remontów awaryjnych podczas kampanii remontowych
- Doradztwo techniczne – analiza przyczyn zużycia, optymalizacja trwałości oraz nadzór nad zabudową ceramiki piecowej
Piece i urządzenia przemysłowe
Cyklony górne
Górne cyklony odgrywają istotną rolę w procesie produkcji klinkieru, zapewniając odpowiednie wymieszanie, przesypanie i dystrybucję składników surowcowych. W tej strefie materiał jest stopniowo podgrzewany, a temperatury mogą sięgać do 600°C. Proces prowadzony jest w trybie ciągłym, co wymaga zastosowania trwałych i odpornych na zużycie materiałów ogniotrwałych. Pod względem zabudowy ogniotrwałej cyklon można podzielić na trzy główne strefy: sklepienie cyklonu, walczak i stożek. Największym wyzwaniem dla obmurza ogniotrwałego w tej części instalacji jest ścieranie spowodowane intensywnym ruchem surowców, natomiast wpływ wysokiej temperatury jest mniej istotny. Ponieważ cyklony górne podlegają długim cyklom remontowym, trwającym kilkanaście do kilkudziesięciu lat, kluczowe jest zastosowanie trwałych i odpornych materiałów. PCO oferuje rozwiązania ogniotrwałe dostosowane do specyfiki pracy cyklonów górnych. W standardowych warunkach stosuje się cegły szamotowe NORMATON, natomiast tam, gdzie występuje intensywne ścieranie, zalecane są szamoty o zwiększonej odporności EXTRATON. W niektórych przypadkach sprawdzają się również wyłożenia betonowe, zapewniające dodatkową trwałość i stabilność pracy cyklonu.
Zakres: Projektowanie Produkcja Montaż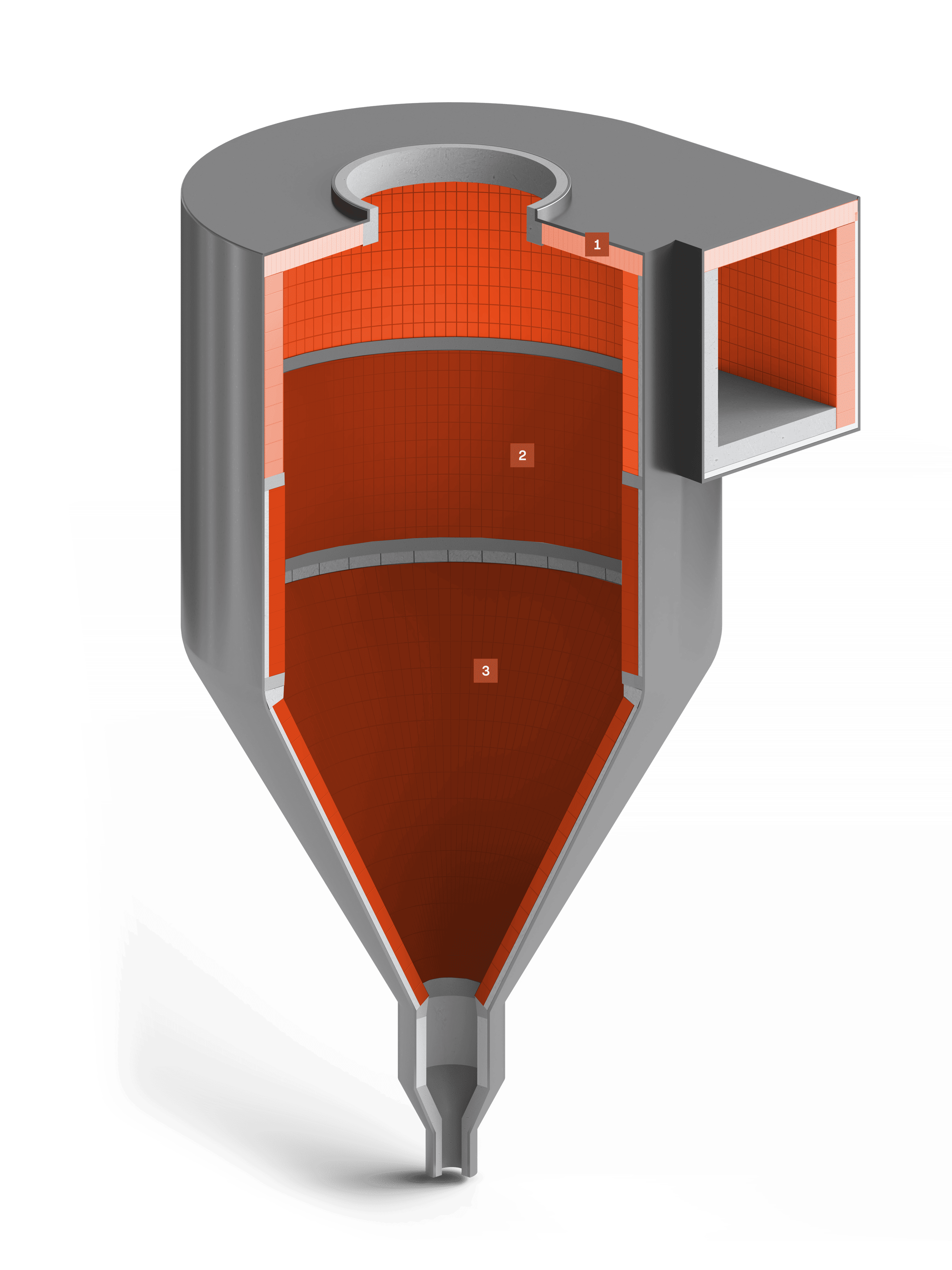
Wymurówka sklepienia cyklonu górnego jest narażona głównie na ścieranie gazowe, spowodowane oddziaływaniem lotnych cząstek wsadu. W tej strefie wpływ temperatury oraz czynników mechanicznych jest niewielki, co przekłada się na stosunkowo łagodne warunki eksploatacyjne. Obmurze sklepienia buduje się w kilku warstwach, z których główną rolę odgrywają warstwy klinów – zarówno robocze, jak i izolacyjne. Wielowarstwowa konstrukcja zapewnia odpowiednią ochronę przed oddziaływaniem gazów oraz minimalizuje zużycie materiału wyłożeniowego. Ze względu na mało wymagające warunki pracy, w tej strefie doskonale sprawdzają się wyroby nisko-glinowe z serii EXTRATON, a także lekkie wyroby izolacyjne ISOLUX. Wybrane materiały gwarantują wystarczającą odporność na ścieranie gazowe, przy jednoczesnym zachowaniu optymalnych właściwości izolacyjnych.
Wymurówka walczaka cyklonu górnego jest narażona na oddziaływanie ścierające oraz mechaniczne, jednak warunki te pozostają na stosunkowo niskim poziomie. Obciążenia mechaniczne są umiarkowane, co pozwala na stosowanie standardowych rozwiązań ogniotrwałych. Obmurze walczaka buduje się podobnie jak w przypadku sklepienia – składa się z kilku warstw, z dominującym zastosowaniem klinów zarówno w warstwach roboczych, jak i izolacyjnych. Taka konstrukcja umożliwia równomierne rozłożenie obciążeń i zapewnia długotrwałą ochronę przed ścieraniem. Przy umiarkowanych warunkach eksploatacyjnych, dla części cylindrycznej walczaka stosuje się te same rozwiązania, co dla sklepienia – wyroby nisko-glinowe EXTRATON oraz lekkie wyroby izolacyjne ISOLUX. Dzięki temu uzyskuje się odpowiednią odporność na ścieranie i mechaniczne oddziaływanie przy zachowaniu efektywności izolacyjnej.
Stożek stanowi fragment cyklonu, który jest najbardziej obciążony mechanicznie spośród wszystkich elementów, choć ogólnie poziom zagrożenia dla wymurówki ogniotrwałej pozostaje niski. Wynika to z kształtu strefy, który wpływa na intensywność oddziaływania czynników mechanicznych. Ze względu na specyfikę geometryczną stożka, obmurze wykonuje się z betonu, co umożliwia lepsze dopasowanie materiału do trudnego kształtu i ułatwia proces murowania. Konstrukcja ta musi uwzględniać konieczność równomiernego rozprowadzenia materiału na nieregularnych powierzchniach.
W czym pomagamy
Jeżeli chciałbyś uzyskać darmową poradę albo zapytać o dobór wyłożenia ogniotrwałego, zostaw nam swoje dane, a zadzwonimy do Ciebie!
Skontaktuj sięJak zminimalizować odłupywanie powierzchni cegieł ogniotrwałych przy szybkim cyklu termicznym?
Który beton naprawczy będzie najbardziej odporny na ścieranie przez cząstki lotne?
Jak zabezpieczyć wyłożenie ceramiczne przed korozją wywołaną alkaliami i atakiem solnym?
Cyklony dolne
Cyklony dolne odgrywają kluczową rolę w procesie produkcji klinkieru, zapewniając intensywne mieszanie, przesypanie i dystrybucję składników surowcowych. W tej strefie temperatury mogą dochodzić nawet do 950°C, co oznacza, że mieszanka jest poddawana wyższemu zakresowi temperatur niż w cyklonach górnych. Istotnym aspektem pracy cyklonów dolnych jest częściowa prekalcynacja kamienia wapiennego, co przyczynia się do zwiększenia efektywności późniejszych etapów procesu. Pod względem zabudowy ogniotrwałej cyklony dolne składają się ze sklepienia, walczaka oraz stożka dolnego. Obmurze ogniotrwałe w tej części instalacji jest narażone na znacznie bardziej agresywne warunki niż w cyklonach górnych. W standardowych warunkach stosuje się cegły wieloszamotowe z dodatkiem andaluzytu i węglika krzemu z linii EXTRATON i ABRAL, które zapewniają wysoką odporność na ścieranie i działanie alkaliów. W przypadku zastosowania wyłożeń betonowych rekomendowane są materiały GELCAST, MULCAST i NxGel, które wykazują wysoką odporność na działanie paliw alternatywnych oraz agresywne środowisko chemiczne.
Zakres: Projektowanie Produkcja Montaż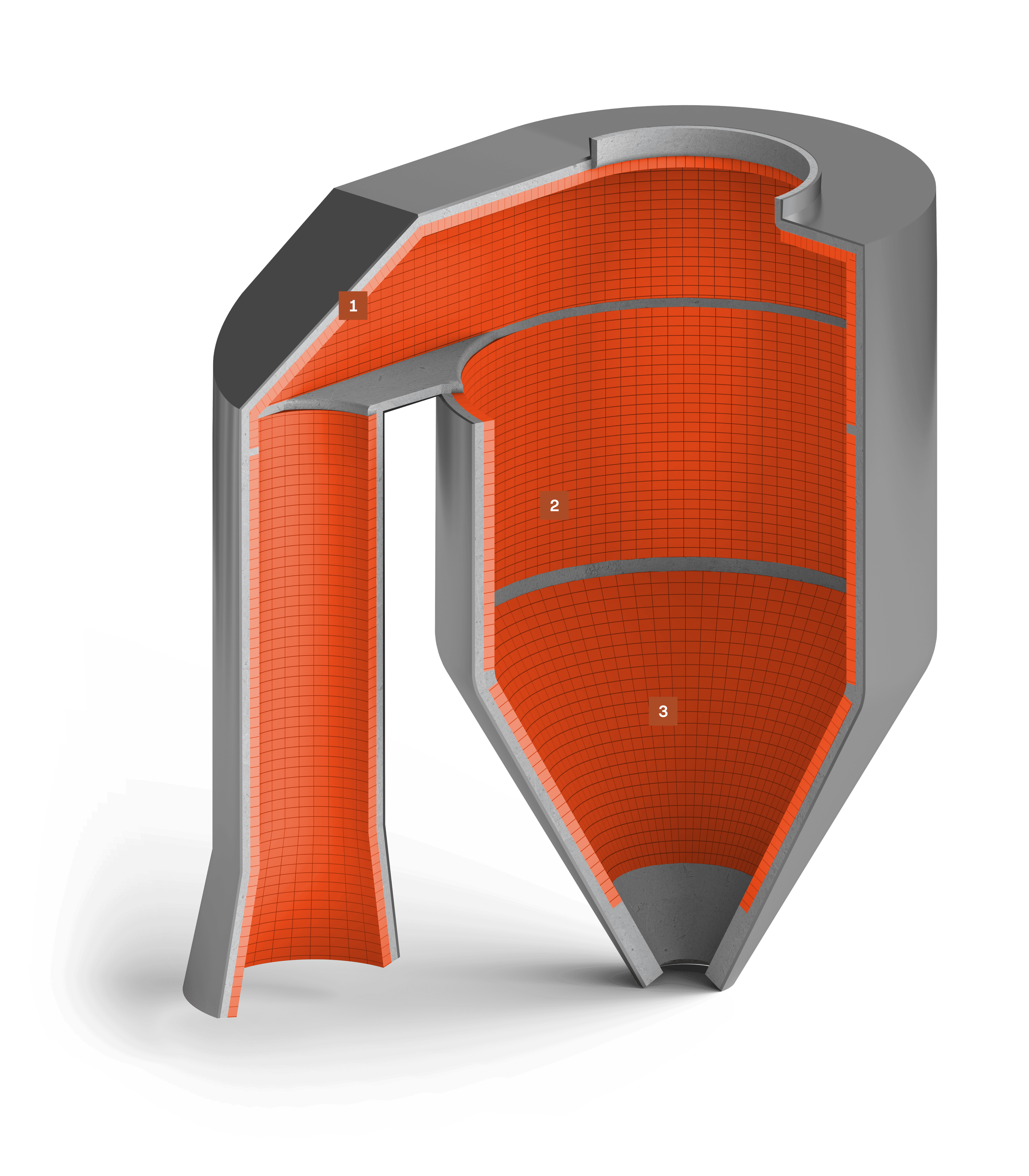
Wymurówka sklepienia cyklonu dolnego jest narażona przede wszystkim na ścieranie gazowe, wynikające z oddziaływania lotnych cząstek wsadu. Choć wpływ temperatury i czynników mechanicznych jest stosunkowo niewielki, warunki pracy są bardziej wymagające niż w standardowych cyklonach górnych. Dodatkowo, obmurze musi stawiać czoła atakom chemicznym oraz zjawisku zarastania napiekami, co podnosi ryzyko degradacji wyłożenia. Obmurze sklepienia buduje się warstwowo – składa się z kilku nakładających się warstw, w których kluczową rolę odgrywają kliny wykorzystywane zarówno w warstwach roboczych, jak i izolacyjnych. Taka struktura pozwala na stopniowe rozłożenie obciążeń oraz zapewnia lepszą ochronę przed oddziaływaniem czynników chemicznych i ścierających.
Wymurówka walczaka cyklonu dolnego jest narażona na kombinację oddziaływań – ścieranie, działanie mechaniczne oraz agresywny atak chemiczny, w tym oddziaływanie alkaliów. Takie wielokierunkowe obciążenia wymagają, aby wyłożenie było odporne zarówno na intensywne zużycie mechaniczne, jak i na degradację chemiczną, co czyni warunki eksploatacyjne tej strefy bardziej wymagającymi. Obmurze walczaka, podobnie jak w przypadku sklepienia, wykonuje się z kilku warstw, przy czym dominującą rolę odgrywają kliny – stosowane w warstwach roboczych oraz izolacyjnych. Wielowarstwowa budowa umożliwia równomierne rozłożenie zarówno obciążeń mechanicznych, jak i chemicznych, co pozwala na wydłużenie okresu eksploatacji wyłożenia.
Stożek, jako fragment cyklonu dolnego, jest najbardziej obciążoną strefą pod względem oddziaływań mechanicznych, chemicznych oraz ściernych. Ze względu na trudności wynikające z nietypowego kształtu stożka oraz utrudnioną technologię murowania, obmurze w tej strefie wykonuje się z betonu. Takie rozwiązanie pozwala na precyzyjne dopasowanie materiału do skomplikowanej geometrii stożka, co minimalizuje ryzyko powstawania nierównomiernych naprężeń i miejscowych uszkodzeń. W strefie stożka kluczowym aspektem jest zapewnienie odporności na zarówno mechaniczne, jak i chemiczne oraz ścierne obciążenia.
W czym pomagamy
Jeżeli chciałbyś uzyskać darmową poradę albo zapytać o dobór wyłożenia ogniotrwałego, zostaw nam swoje dane, a zadzwonimy do Ciebie!
Skontaktuj sięKtóry beton ogniotrwały oferuje optymalny balans między odpornością na ścieranie a tolerancją na szok termiczny?
Jak skompensować różnicę rozszerzalności między warstwami ceramiki a stalową obudową, aby uniknąć pęknięć?
Jak zminimalizować zalepienia z pyłu na wymurówce ogniotrwałej?
Kalcynator
Kalcynator, wykorzystywany głównie do wstępnego podgrzania i kalcynacji surowców wapiennych, przenosi część procesu spalania oraz dekarbonizacji z pieca obrotowego do wieży wymienników. Dzięki zastosowaniu paliw alternatywnych, kalcynator pozwala na zmniejszenie emisji gazów i obniżenie kosztów eksploatacji. Niemniej jednak, warunki pracy są zdecydowanie trudniejsze, co wymaga stosowania zaawansowanych materiałów ogniotrwałych. Zakres temperatur pracy wynosi od 800°C do 1100°C, a kanał kalcynatora jest narażony na działanie wysokich temperatur oraz czynników korozyjnych (SOx, NOx, alkaliów, chloru i siarki), które prowadzą do abrazyjnego zużycia wymurówki. Z tego względu stosuje się betony ogniotrwałe niskocementowe lub bezcementowe z dodatkiem cyrkonu i węglika krzemu, a w przypadku napraw betony natryskiwane. W zabudowie z cegieł zalecane są wyroby wysokoglinowe, odporne na atak chemiczny, wysokie temperatury oraz szok termiczny. Wymurówka kalcynatora jest kilkuwarstwowa, z warstwą roboczą, ochronną i izolacyjną, co zapewnia jej trwałość w ekstremalnych warunkach. Cykl remontowy wynosi kilka lat, w zależności od warunków eksploatacji i udziału paliw alternatywnych.
Zakres: Projektowanie Produkcja Montaż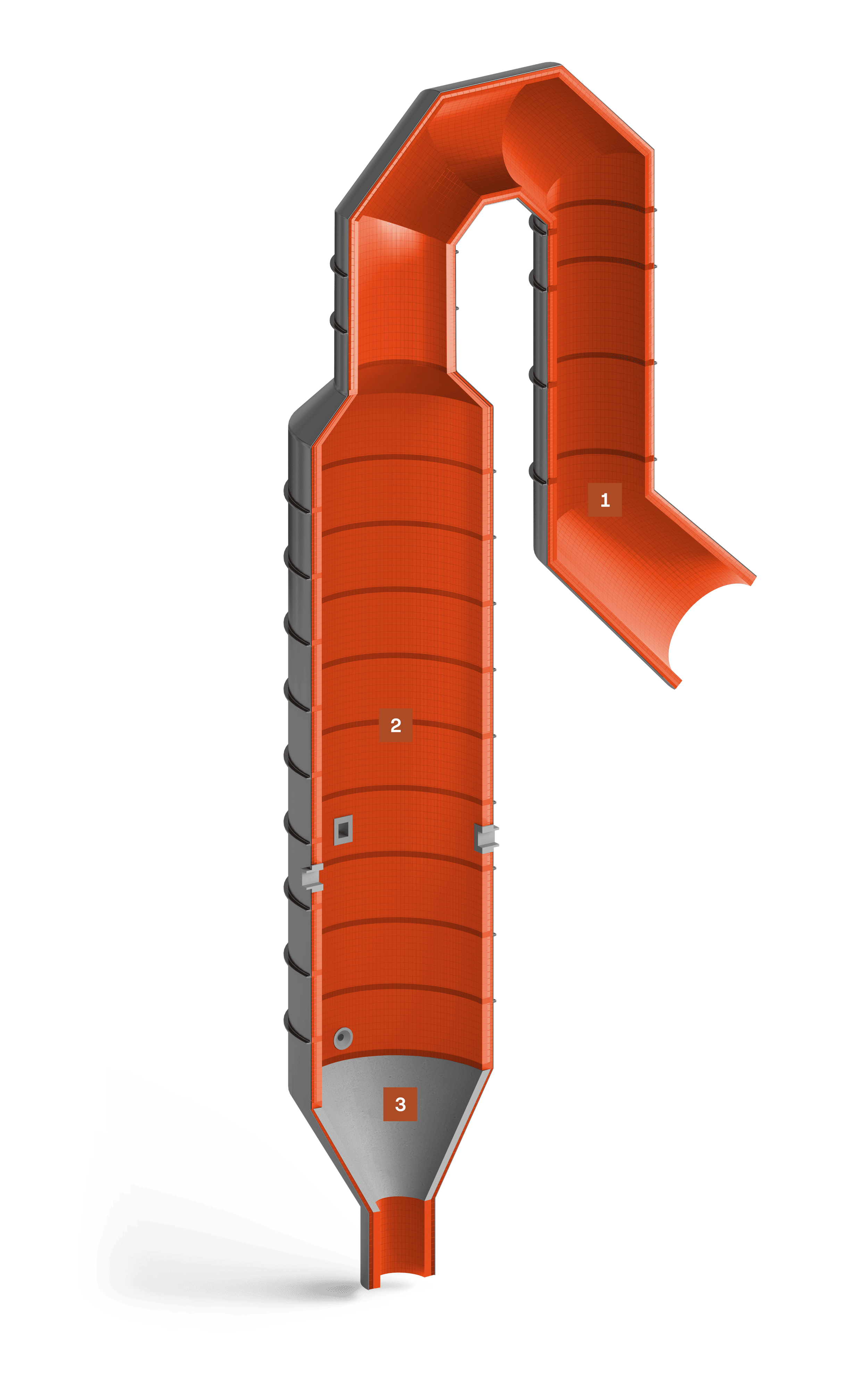
W tej strefie panują temperatury około 700 – 900 °C. Głównym czynnikiem ryzyka dla wymurówki jest abrazja mechaniczna i erozja chemiczna. Jest to spowodowane wlotem mączki. Niekiedy obserwuje się powstawanie narostów na wymurówce, głównie pochodzące z siarki i chloru (w przypadku paliw alternatywnych). Preferuje się zabudowę z betonów ogniotrwałych wysokoglinowych z udziałem ZrO lub SiC. Jeżeli zabudowa wykonana jest z cegieł, należy rozważyć cegły wysokoglinowe odporne na ścieranie i szok termiczny.
W tej strefie panują temperatury przekraczające 1000 °C, w obszarze palników miejscowo nawet 1200 °C. Ta strefa to jedno z najtrudniejszych miejsc pracy dla wyrobów ogniotrwałych w całej instalacji cementowniczej. Wynika to z charakterystyki procesu prowadzanego w tym urządzeniu - w kalcynatorze stosuje się zazwyczaj 100% paliw alternatywnych i towarzyszy temu atak alkaliów na wymurówkę ogniotrwałą. Zarówno betony i cegły pracujące w tej strefie powinny być wysokoglinowe z dodatkami poprawiającymi odporność na atak chemiczny i ścieranie.
W tej strefie panują nadal wysokie temperatury w granicach 1000 °C. Głównym czynnikiem ryzyka są natomiast alkalia, które pojawiają się w wyniku spalania w procesie kalcynacji w strefie powyżej. Stosuje się tu niskocementowe i bezcementowe betony wysokoglinowe. W przypadku wyłożenia z cegieł, polecane są wysokoglinowe cegły z dodatkami węglika krzemu. Wymurówka często zarasta napiekami chemicznymi które są pochodnymi stosowania paliw alternatywnych – są one dotkliwe do tego stopnia, że muszą być czyszczone powietrzem lub wodą w trakcie remontów bieżących. Wyłożenie musi być też odporne na uderzenie mechaniczne, ponieważ obrywające się napieki z wyższych stref spadają na pochyłą strefę przewężenia położoną u dołu kalcynatora.
W czym pomagamy
Jeżeli chciałbyś uzyskać darmową poradę albo zapytać o dobór wyłożenia ogniotrwałego, zostaw nam swoje dane, a zadzwonimy do Ciebie!
Skontaktuj sięJak dobrać torkret który będzie odporny na ścieranie przez spieczony klinkier i korozję CO₂?
Który typ materiału ogniotrwałego sprawdzi się najlepiej w warunkach krótkich cyklów pracy i przy ryzyku szoku termicznego?
Jak zaprojektować wyłożenie i uwzględnić pozycję palnika, aby uniknąć miejscowych przegrzań na pancerzu?
Kanał Trzeciego Powietrza (TAD)
W kanale trzeciego powietrza (TAD), w którym temperatura zmienia się od 1000°C w strefie gorącej do 600°C w strefie chłodnej, panują trudne warunki pracy. Kanał ten dostarcza dodatkowy strumień powietrza do procesu, co nie tylko poprawia efektywność spalania, ale również umożliwia precyzyjne kontrolowanie temperatury wewnętrznej w piecu. Aby zapewnić optymalną wydajność procesu, istnieje możliwość dynamicznej regulacji kluczowych parametrów, takich jak przepływ powietrza, temperatura czy ciśnienie, przy zastosowaniu zaawansowanych systemów monitorowania i sterowania.
Zakres: Projektowanie Produkcja Montaż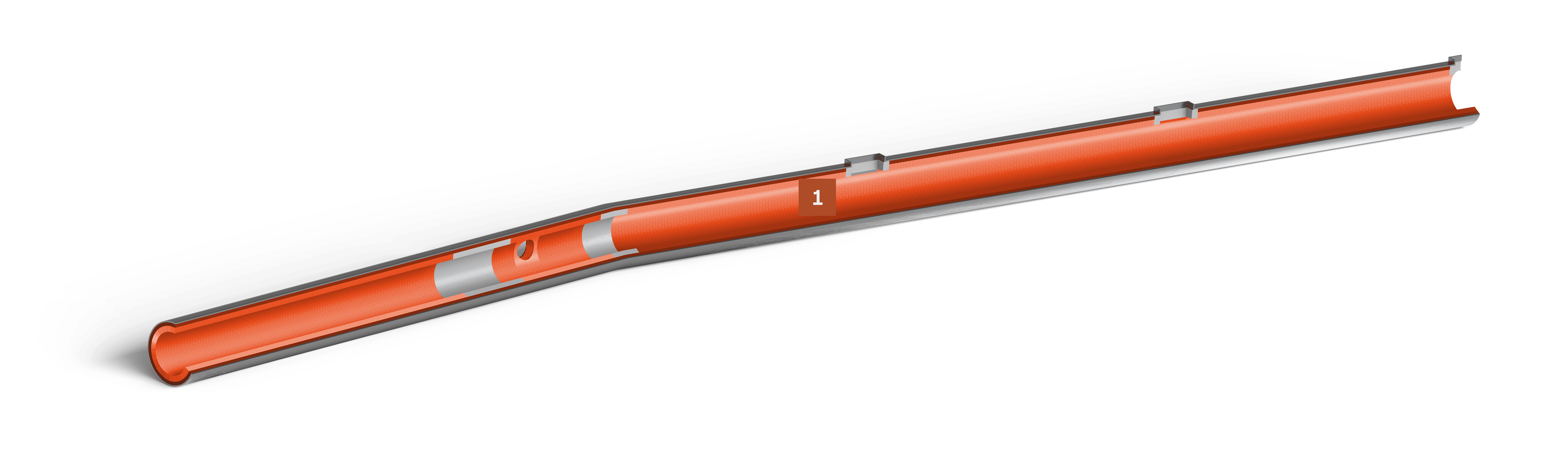
Trudność pracy ceramiki kanale trzeciego powietrza polega na małej średnicy kanału, co potęguje wpływ abrazyjnego środowiska – cząstki przelatują przez rurę pod wysokim ciśnieniem. Aby zwiększyć trwałość, PCO zaleca stosowanie cegieł formowanych EXTRATON oraz betonu szamotowego PCOCAST z dodatkami zwiększającymi odporność na ścieranie, takimi jak węglik krzemu lub cyrkon. W przypadku jeszcze trudniejszych warunków pracy, takich jak wyższe ciśnienie lub wyższe temperatury, zaleca się zastosowanie cegieł szamotowych z węglikiem krzemu klasy ABRAL.
W czym pomagamy
Jeżeli chciałbyś uzyskać darmową poradę albo zapytać o dobór wyłożenia ogniotrwałego, zostaw nam swoje dane, a zadzwonimy do Ciebie!
Skontaktuj sięJak dobrać układ warstwowy wyłożenia, aby otrzymać oczekiwaną temperaturę na pancerzu (np. poniżej 200 °C)?
Jaka zaprawa ogniotrwała zapewni wytrzymałość łączeń warstwy roboczej przy wysokim ciśnieniu przepływającego powietrza?
Który materiał będzie odpowiedni do zabudowy kolan kanału?
Rura wzniosu i komora wlotowa do pieca
Rura wzniosu i komora wlotowa to elementy instalacji cementowniczej odpowiadające za przenoszenie wstępnie podgrzanego materiału z cyklonów do pieca obrotowego, gdzie surowiec jest dalej podgrzewany. Zakres temperatur pracy to od około 500°C w górnej części rury wzniosu do 1100°C na przejściu do pieca obrotowego. Ponadto, komora wlotowa (nazywana też komorą dymową) odbiera gorące spaliny z pieca i przekazuje je do układu cyklonów, umożliwiając recyrkulację ciepła. Czynnikami ryzyka dla poprawnej pracy wymurówki są agresywne gazy (atak alkaliów), udary mechaniczne oraz ścieranie spowodowane przesuwaniem materiału, co staje się szczególnie problematyczne w instalacjach z kalcynatorem, gdzie udział paliw alternatywnych jest większy. Dlatego wyłożenie ogniotrwałe powinno charakteryzować się niską porowatością i wysoką odpornością na ścieranie. PCO Żarów oferuje kompletne rozwiązania od projektu do montażu, dostarczając cegły i betony ogniotrwałe o zawartości Al₂O₃ w zakresie od 30% do 60%, wzbogacone o dodatki zwiększające odporność na czynniki chemiczne i ścieranie.
Zakres: Projektowanie Produkcja Montaż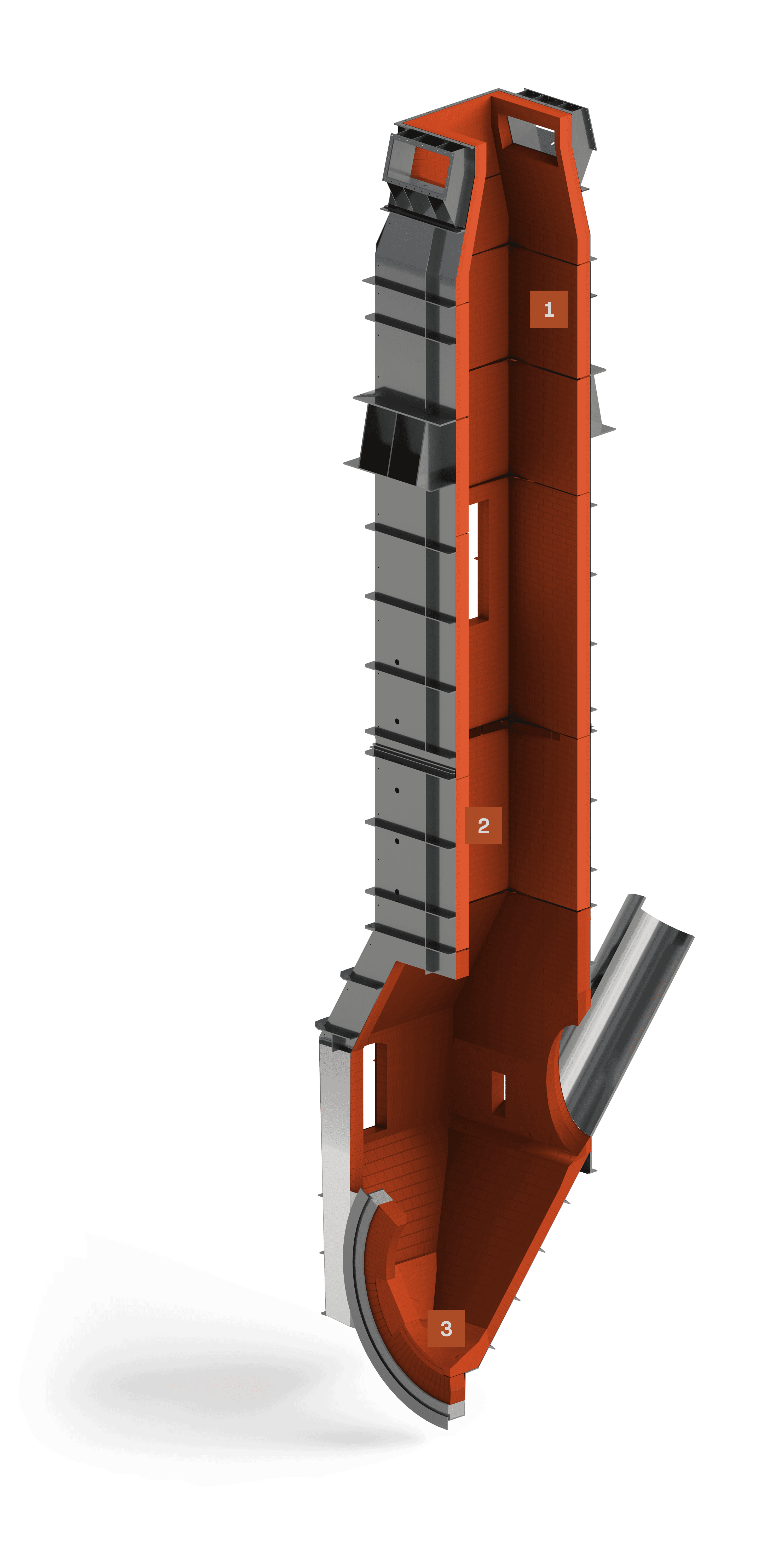
W górnej części rury wzniosu, gdzie temperatury nie przekraczają 700°C, stosuje się wyroby szamotowe jako warstwę roboczą. PCO Żarów rekomenduje produkty EXTRATON lub ABRAL, które charakteryzują się podwyższoną odpornością na ścieranie. W przypadku bardziej wymagających warunków możliwe jest również zabudowanie tej strefy cegłą wysokoglinową boksytową – BAUXITEX, która dodatkowo zwiększa ochronę wyłożenia.
W dolnej części rury wzniosu, gdzie występują trudniejsze warunki pracy, wymurówka musi sprostać wyższej temperaturze – sięgającej do 1100°C – oraz intensywnemu atakowi chemicznemu. Zazwyczaj stosuje się tu wyroby wysokoglinowe, oparte o surowce andaluzytowe lub boksytowe, uzupełnione o dodatki zwiększające odporność mechaniczną i chemiczną. PCO Żarów rekomenduje produkty klasy ABRAL, ANDALUX lub betony ultraniskocementowe NxGel, dedykowane do procesu szybkiego wygrzewania, co gwarantuje optymalną ochronę wyłożenia w tej wymagającej strefie.
Komora wlotowa (komora dymowa) to miejsce, gdzie głównym wpływem procesu na wymurówkę jest atak chemiczny z gorących spalin i gazów. Ponadto, wymurówka jest poddana udarowi mechanicznemu – wsad spada z rury wzniosu do komory, gdzie przesuwany jest do pieca obrotowego. To skutkuje znacznym wycieraniem wyłożenia ceramicznego. Częstym problemem jest zarastanie wyłożenia napiekiem z surowca i miejscowe blokowanie kanału. Wyłożenie ceramiczne powinno zawierać dodatki węglika krzemu lub cyrkonu, które uodpornią ją na udar mechaniczny i zaklejanie surowca (nadają cegłom i betonom niską porowatość i niezwilżalność) po to, aby zminimalizować powstawanie napieków i umożliwić swobodne przemieszczanie mączki wapiennej do pieca obrotowego.
W czym pomagamy
Jeżeli chciałbyś uzyskać darmową poradę albo zapytać o dobór wyłożenia ogniotrwałego, zostaw nam swoje dane, a zadzwonimy do Ciebie!
Skontaktuj sięKtóry materiał poprawi odporność wyłożenia na działanie chemicznych produktów procesu?
Jak ograniczyć erozję wyłożenia ogniotrwałego na przejściu z kanału do komory?
Który materiał ogniotrwały sprawdzi się pracy w warunkach szoku termicznego?
Palnik główny
W tej strefie, gdzie temperatura może przekraczać 1500°C, obmurza narażone są na gwałtowne zmiany ciepła, promieniowanie cieplne oraz działanie utleniaczy i związków siarki, co wymaga stosowania materiałów o wyjątkowej odporności na korozję chemiczną i szok termiczny. Wyłożenie ceramiczne palnika zapewnia nie tylko ochronę stali przed degradacją, ale również efektywne zarządzanie przepływem ciepła, minimalizując straty termiczne i zwiększając efektywność procesu spalania. W tej strefie wyłożenie ogniotrwałe jest remontowane stosunkowo często – cykl remontowy wynosi kilka miesięcy do maksymalnie jednego roku.
Zakres: Projektowanie Produkcja Montaż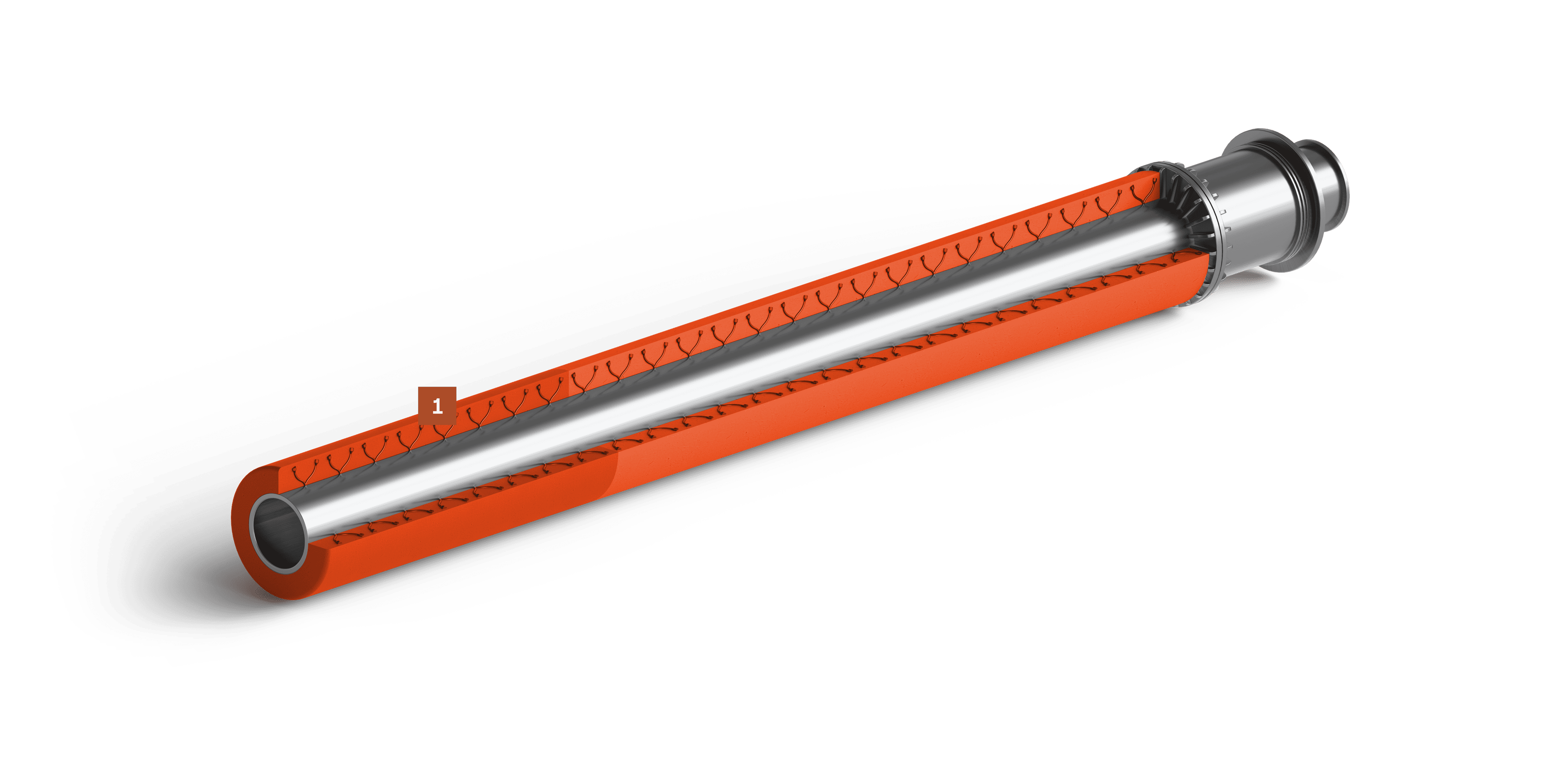
W tej strefie wyłożenie ogniotrwałe jest narażone na bardzo wysokie temperatury oraz agresywne oddziaływanie paliwa alternatywnego, co skutkuje koniecznością częstych remontów. Aplikacja wyłożenia w strefie płomienia wiąże się z trudnościami, szczególnie przy procesie odlewania betonu na palniku. Wymaga to nie tylko zastosowania odpowiednich technologii, ale również dużego doświadczenia od murarzy. Kluczowe jest uzyskanie homogenicznej konsystencji betonu, która gwarantuje równomierne rozprowadzenie materiału oraz zapewnia jego szybkie wygrzanie, co jest niezbędne do zachowania ciągłości procesu pracy pieca. Ze względu na ekstremalne warunki pracy w strefie płomienia, materiał ogniotrwały musi charakteryzować się bardzo wysoką odpornością na szok termiczny i agresywne działanie paliw alternatywnych.
W czym pomagamy
Jeżeli chciałbyś uzyskać darmową poradę albo zapytać o dobór wyłożenia ogniotrwałego, zostaw nam swoje dane, a zadzwonimy do Ciebie!
Skontaktuj sięJak zaprojektować kształtki palnikowe by uniknąć przepalenia?
Jak dobrać materiał ceramiczny który najlepiej wytrzyma naprężenie termiczne?
Jak zaplanować cykl inspekcji wyłożenia palnika aby w porę wykryć nadmierne zużycie wyłożenia?
Piec obrotowy
Główną rolą pieca obrotowego w procesie produkcji klinkieru cementowego jest podgrzewanie wsadu surowcowego do bardzo wysokich temperatur (1350–1450°C), co prowadzi do jego kalcynacji i reakcji chemicznych tworzących minerały klinkierowe. Kluczowe czynniki zużycia wymurówki ogniotrwałej pieca obrotowego to: ścieranie, obciążenia termiczne pochodzące zarówno od wsadu, jak i palnika, obciążenia mechaniczne związane z pracą pancerza stalowego pieca, korozja chemiczna wynikająca z kontaktu ze wsadem, gazami oraz żużlami powstającymi w wyniku spalania paliw alternatywnych, a także z obecności agresywnych związków chemicznych. Dla pieców obrotowych PCO oferuje kompleksowy zakres materiałów i usług. W ofercie znajdują się wysokoglinowe materiały ogniotrwałe z dodatkiem SiC, charakteryzujące się zwiększoną odpornością na korozję chemiczną, ścieranie i szoki termiczne, wyroby andaluzytowe na wiązaniu chemicznym o wysokiej trwałości, materiały szamotowe i wysokoglinowe o podwyższonej odporności na ścieranie i korozję chemiczną.
Zakres: Projektowanie Produkcja Montaż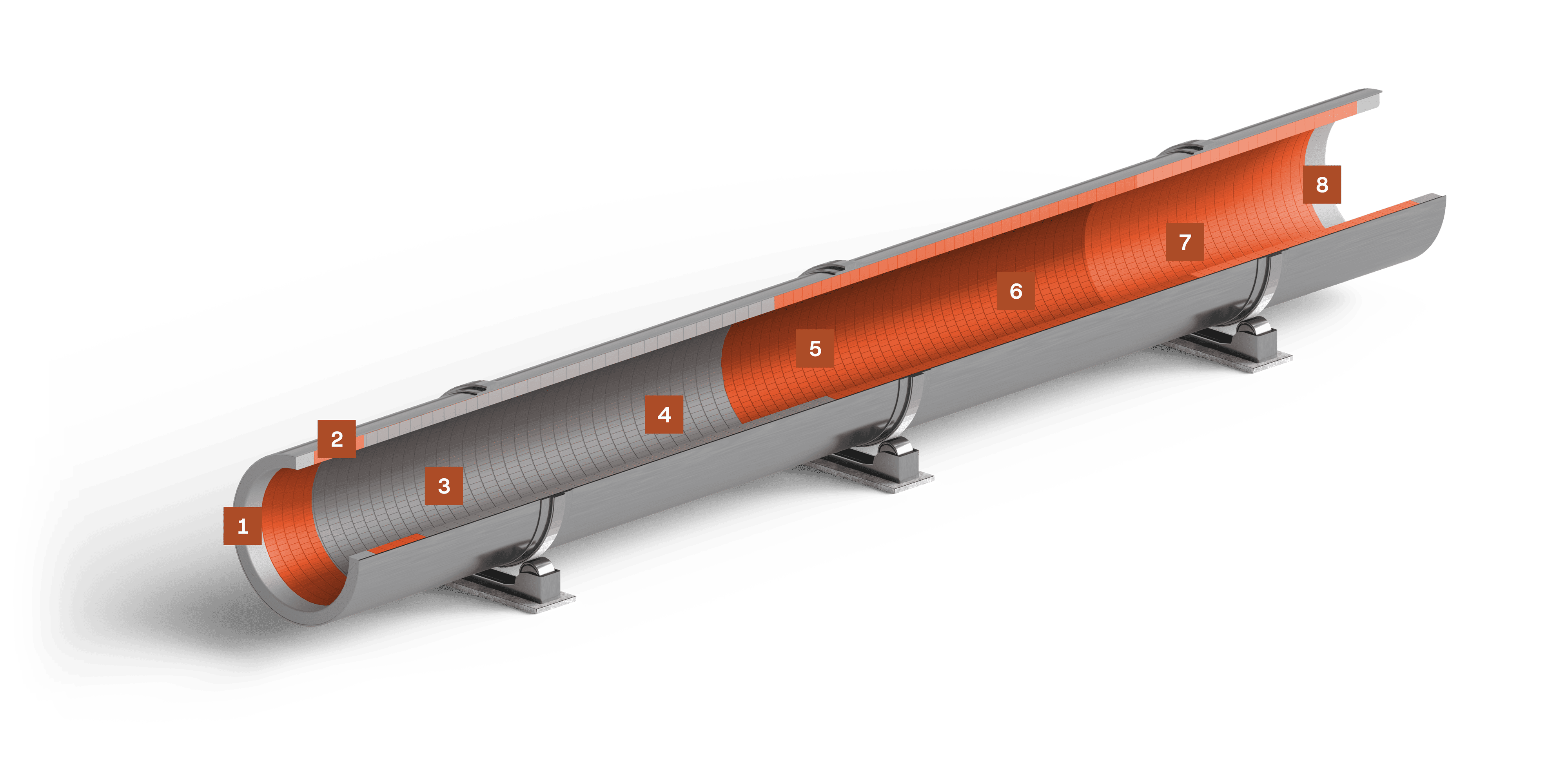
Strefa końcowa pieca – tzw. „nose ring” – charakteryzuje się warunkami zbliżonymi do strefy wylotowej. Panują tu zmienne temperatury oraz wysoki nacisk przetwarzanego wsadu, co wymaga zastosowania materiałów o doskonałej wytrzymałości mechanicznej. Konstrukcja pieca obrotowego przewiduje stosowanie wyrobów monolitycznych, które są odlewane z betonu bezpośrednio na miejscu podczas remontów. Kluczową cechą tych materiałów jest odporność na ściskanie oraz ścieranie, co zapewnia integralność konstrukcyjną w warunkach intensywnego obciążenia. Polecane są tu wysokoglinowe betony klasy MULCAST i niskocementowe PCOCAST.
W strefie chłodzenia głównym wyzwaniem dla materiałów ogniotrwałych jest udar mechaniczny, wynikający z pękającego klinkieru, który zmienia swoją objętość wskutek gwałtownych zmian temperatury. Temperatury w tym obszarze są zmienne i mieszczą się w zakresie 900 – 1100 °C. Obmurze składa się z pojedynczej warstwy klinów, a kluczowe właściwości wymagane od materiałów ogniotrwałych to wysoka odporność na szok termiczny oraz wyjątkowa wytrzymałość mechaniczna na udary i ścieranie.
W dolnej strefie przejściowej, klinkier spieczony w poprzedniej strefie ulega stopniowemu schładzaniu, przy czym temperatury spadają do około 1200 °C. Pomimo obniżenia temperatury, nadal stosuje się materiały ogniotrwałe o wysokiej odporności na dynamiczne zmiany temperatury. Na tym etapie przeważają wyroby magnezjowo-spinelowe, które gwarantują ciągłość ochrony obmurza przy jednoczesnym ograniczaniu naprężeń termicznych.
Strefa palenia to obszar o najwyższych osiąganych temperaturach, dochodzących do 1500 °C, gdzie następują kompletne przemiany chemiczne. Wsadu z kamienia wapiennego poddawanego jest intensywnym reakcjom, prowadzącym do formowania klinkieru. W tej strefie zaleca się stosowanie wyrobów magnezytowych, które dzięki swoim właściwościom zapewniają odpowiednią odporność na ekstremalne warunki termiczne i chemiczne zachodzące podczas spalania.
W górnej strefie przejściowej obserwuje się bardzo silne oddziaływanie termiczne, przy temperaturach przekraczających 1200 °C. Strefa charakteryzuje się niestabilnymi i zmiennymi warunkami, a obmurze, wykonane z pojedynczej warstwy klinów, musi być odporne na gwałtowne zmiany ciepła. W tym obszarze przeważnie stosuje się materiały magnezjowo-spinelowe, natomiast na granicy przejścia w strefę bezpieczeństwa zabudowuje się najwyższej klasy materiały glinokrzemianowe, zapewniające optymalną ochronę przed szokami termicznymi.
W strefie bezpieczeństwa panują temperatury przekraczające 1000 °C, co sprzyja rozkładowi kamienia wapiennego. Warunki w tej strefie są zmienne i silnie zależą od prowadzonego procesu, szczególnie przy zwiększonym udziale RDF w paliwie. Obmurze, zbudowane z pojedynczej warstwy klinów, narażone jest na działanie alkaliów, płynnych eutektyków, niestabilnych naprężeń oraz agresywne oddziaływanie chemiczne i termiczne ze wsadu i paliw alternatywnych. Dobór gatunkowy materiałów ogniotrwałych musi być elastyczny, aby sprostać zmiennym warunkom operacyjnym. Dla tej strefy należy stosować wyroby wysokoglinowe z udziałem SiC klasy ABRAL lub ANDALUX, BAUXITEX na wiązaniu chemicznym.
W strefie kalcynacji pieca obrotowego, oprócz intensywnego ścierania mechanicznego wywołanego ruchem wsadu, występuje dodatkowe oddziaływanie związków alkalicznych pochodzących z surowców i paliw. Temperatury w tej części pieca utrzymują się w granicach 1000–1100 °C. Obmurze stanowi pojedyncza warstwa klinów. Kluczowym wymaganiem dla materiałów ogniotrwałych stosowanych w tej strefie jest wysoka odporność mechaniczna oraz odporność na korozję, co zapewnia niezakłóconą pracę systemu przy zmiennych warunkach procesowych. W zależności od warunków procesowych w tej aplikacji sprawdzają się produkty z grupy ABRAL, charakteryzujące się podwyższoną odpornością na korozję i ścieranie mechaniczne.
W tej strefie, będącej początkiem zabudowy pieca, głównym zagrożeniem jest intensywne ścieranie mechaniczne, wynikające z ruchu przesuwającego się wsadu piecowego. Aby sprostać temu wyzwaniu, stosuje się betony odporne na ścieranie. Kluczowe jest wykorzystanie betonu wysokoglinowego; rekomendowanym produktem jest beton średniocementowy klasy MULCAST lub betony bezcementowe GELCAST zapewniające wystarczającą wytrzymałość i odporność na mechaniczne uszkodzenia.
W czym pomagamy
Jeżeli chciałbyś uzyskać darmową poradę albo zapytać o dobór wyłożenia ogniotrwałego, zostaw nam swoje dane, a zadzwonimy do Ciebie!
Skontaktuj sięJak zoptymalizować dobór formatów i proporcję zabudowy cegieł, by zmniejszyć tworzenie się pierścieni i napieków klinkieru?
Który materiał zabudować w piecu opalanym paliwem z wysokim udziałem RDF?
Jak uwzględnić nieregularny kształt pancerza przy projektowaniu wyłożenia?
Chłodnik i głowica pieca
Chłodnik i głowica pieca mają za zadanie schłodzenie klinkieru po wyjściu z pieca obrotowego. W głowicy temperatura może sięgać 1100°C, natomiast w chłodniku stopniowo spada – od około 800°C w strefie gorącej do nawet 100°C w strefie chłodnej. W konstrukcji chłodnika wyróżnia się strefę gorącą, strefę chłodną, strop oraz bullnose ring. Glinokrzemianowe wyroby ogniotrwałe stosuje się we wszystkich obszarach chłodnika. Na zużycie wyłożenia głowicy chłodnika główny wpływ mają udary termiczne spowodowane wybuchającym klinkierem oraz ścieranie wynikające z jego przesuwu. Dodatkowe zagrożenia stanowią szoki termiczne oraz destrukcyjne oddziaływanie chemiczne i ścierne gazów procesowych Strefą szczególnie narażoną na zużycie jest bullnose, który znajduje się w bezpośrednim sąsiedztwie wysokotemperaturowych gazów i klinkieru. PCO oferuje szeroką gamę materiałów ogniotrwałych do zabudowy chłodnika, w tym betony ogniotrwałe, prefabrykaty betonowe oraz cegły boksytowe.
Zakres: Projektowanie Produkcja Montaż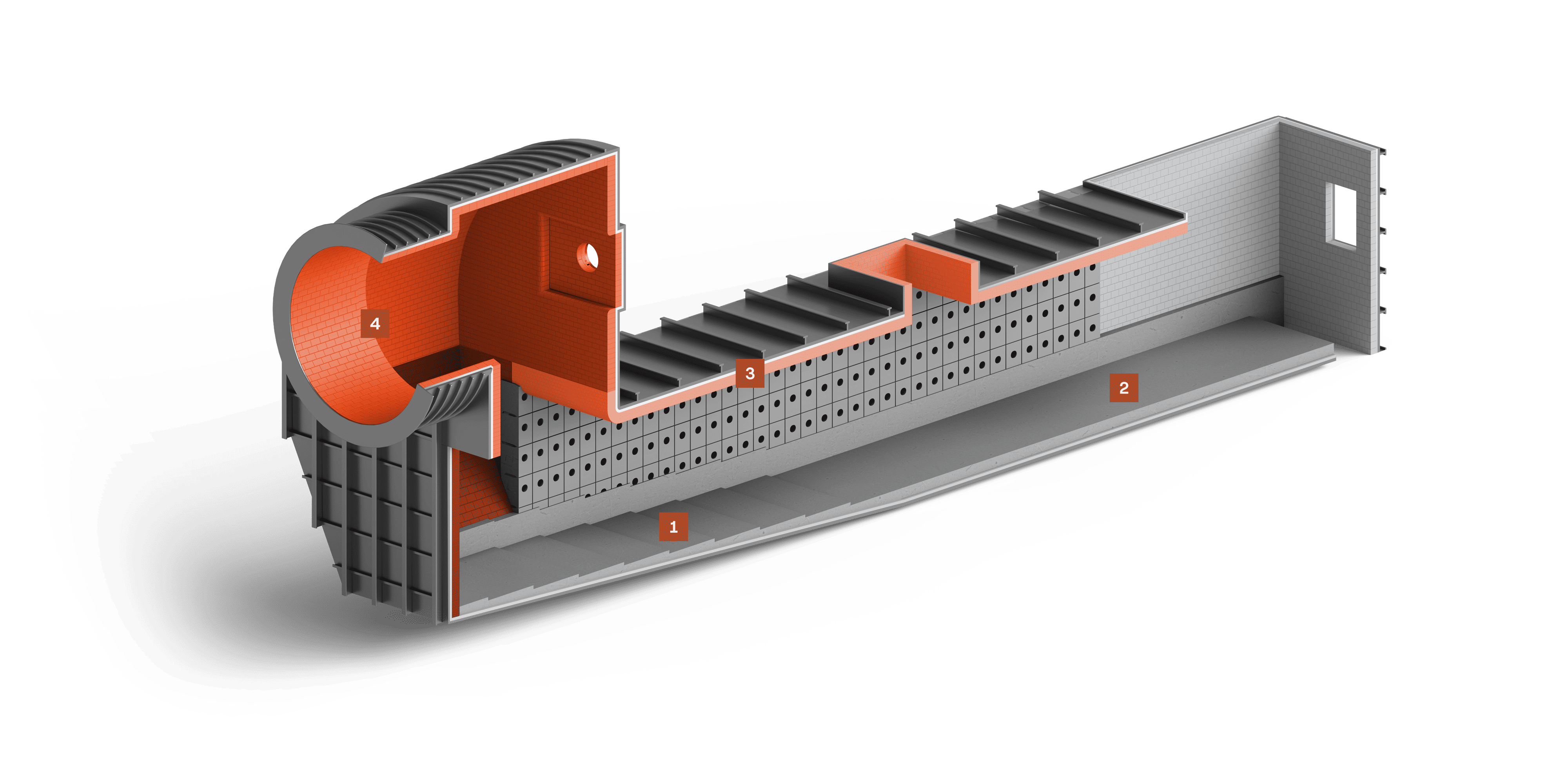
W strefie gorącej chłodnika panują temperatury dochodzące do 1000 °C, które gwałtownie spadają w kierunku przesuwającego się rusztu. Takie warunki generują silne szoki termiczne, a na łóżku klinkierowym głównym zagrożeniem dla wyłożenia ogniotrwałego jest intensywne ścieranie mechaniczne, wynikające zarówno z ruchu wsadu, jak i oddziaływania dynamicznych przepływów powietrza i pyłów. Obmurze w tej strefie wykonuje się z prefabrykatów betonowych, czyli stosowanych murków oporowych, które zapewniają nie tylko odpowiednią izolację termiczną, ale również stabilność mechaniczną przy zmiennych warunkach temperaturowych. Kluczowym aspektem dla niezawodnej pracy obmurza jest użycie betonu wysokoglinowego, który charakteryzuje się wysoką odpornością na szok termiczny oraz na intensywne ścieranie. Dzięki temu materiał utrzymuje swoje właściwości eksploatacyjne nawet przy gwałtownych spadkach temperatur i obciążeniach mechanicznych.
W strefie chłodnej warunki termiczne są bardzo stabilne, a temperatura nie przekracza 500 °C. Z uwagi na łagodniejsze oddziaływanie temperatur i mniejsze dynamiczne zmiany, ta część chłodnika cechuje się niskim obciążeniem termicznym oraz mechanicznie – co sprawia, że obmurze jest stosunkowo rzadko remontowane. W tej strefie stosuje się obmurze wykonane z betonu natryskowego, który zapewnia spójną i równomierną powierzchnię wyłożenia. Dodatkowo, wzdłuż rusztu realizowane są prefabrykowane murki oporowe, wykonane z niższych gatunków ogniotrwałych, takich jak MULCAST BN45M S5.
Strop, eksploatowany zarówno w strefie gorącej, jak i chłodnej, jest narażony na ścieranie spowodowane oddziaływaniem pyłów lotnych oraz dynamicznymi zmianami temperatur, które występują na całej długości chłodnika. Ceramika ogniotrwała powinna być odporna na ścieranie mechaniczne jak i na zmienne obciążenia termiczne. W przypadku stropu istotne jest, aby zastosowane materiały wykazywały doskonałe właściwości mechaniczne oraz termiczne – zwłaszcza w rejonie strefy gorącej, gdzie dodatki SiC poprawiają wytrzymałość wyłożenia. Natomiast w strefach chłodnych priorytetem jest zapewnienie spójności i trwałości obmurza przy niższych temperaturach, co umożliwia długotrwałą eksploatację bez konieczności częstych remontów.
Głównym zadaniem głowicy pieca jest odzysk klinkieru oraz jego przekazanie do chłodnika, co odbywa się w warunkach intensywnie oddziałujących czynników mechanicznych i termicznych. Szczególną uwagę należy zwrócić na strefę określaną jako Bullnose ring – pionową ścianę, która jest najbardziej narażona na uszkodzenia. W tej strefie wyłożenie ogniotrwałe doświadcza obciążeń mechanicznych wynikających z uderzeń spadającego klinkieru, co w połączeniu z gwałtownymi zmianami temperatury stawia przed materiałami wysokie wymagania. W głowicy pieca obmurze wykonuje się najczęściej z cegieł formowanych, które zapewniają stabilność termiczną i odpowiednią izolację, minimalizując straty ciepła oraz wpływ czynników zewnętrznych. Natomiast w przypadku Bullnose ring, ze względu na ekstremalne obciążenia mechaniczne, stosuje się wysokiej klasy beton ogniotrwały lub prefabrykaty betonowe.
W czym pomagamy
Jeżeli chciałbyś uzyskać darmową poradę albo zapytać o dobór wyłożenia ogniotrwałego, zostaw nam swoje dane, a zadzwonimy do Ciebie!
Skontaktuj sięKtóry beton ogniotrwały zapewni najwyższą odporność na ścieranie w rejonie pierścienia wysadowego (bullnose ring)?
Jak zapobiec uszkodzeniom wyłożenia w warunkach szoku termicznego podczas wahań przepływu chłodniejszego gazu?
Jak zaprojektować prefabrykowane ściany oporowe, aby zabezpieczyć wyłożenie przed wibracjami z rusztu?
Piec szybowy
Piec szybowy, stosowany w technologii produkcji wapna, operuje przy temperaturach często przekraczających 1100°C, przy czym proces kalcynacji wymaga równomiernego i kontrolowanego rozkładu ciepła na całej długości pieca. Wprowadzony do pieca kamień wapienny jest mieszany z koksem lub antracytem, a proces spalania paliwa wytwarza wysoką temperaturę, która umożliwia przekształcenie kamienia wapiennego w wapno, czyli tlenek wapnia (CaO). W przemyśle sody, produkcja wapna odbywa się w piecach działających w nieco niższych temperaturach niż w produkcji wapna klasycznego, co wiąże się z mniejszymi wymaganiami dotyczącymi materiałów ogniotrwałych i systemów grzewczych. W cukrowniach natomiast piece wykorzystywane do przetwarzania wapna są narażone na specyficzne warunki pracy, ponieważ często dochodzi do częstych zmian temperatury i postojów. To wymaga zastosowania wytrzymałych materiałów ogniotrwałych, które będą w stanie wytrzymać cykliczne zmiany temperatury bez nadmiernego zużycia. W tego typu piecach procesy kalcynacji nie zachodzą w sposób ciągły, co różni je od pieców wykorzystywanych w innych branżach, takich jak przemysł wapienniczy czy soda.
Zakres: Projektowanie Produkcja Montaż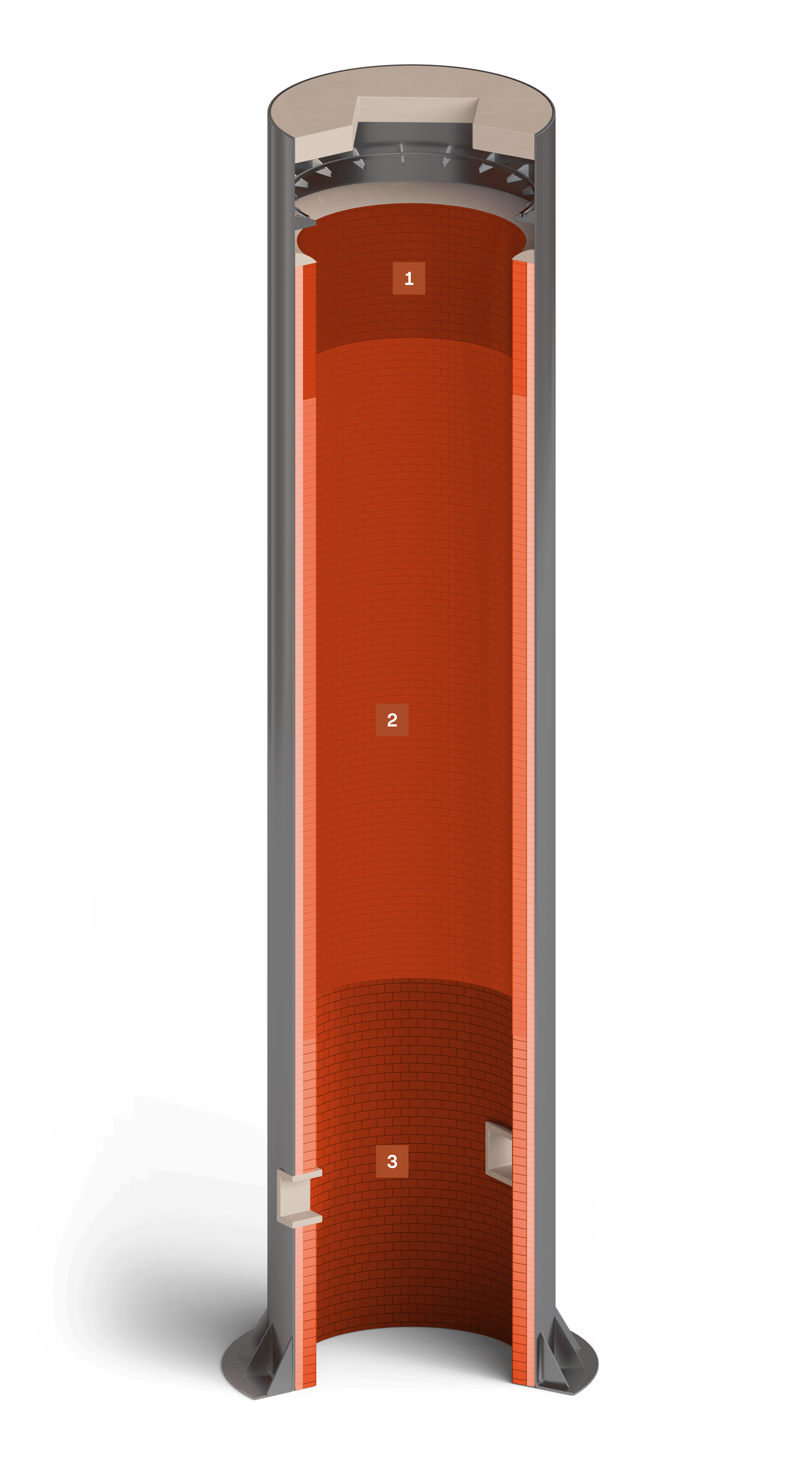
Strefa podgrzewania to obszar, do którego cyklicznie załadowywany jest kamień wapienny zmieszany z paliwem. Proces ten generuje intensywne oddziaływanie ścierające, wynikające z mechanicznego przemieszczania wsadu, przy jednoczesnym występowaniu wysokich temperatur. Materiały użyte w strefie podgrzewania muszą charakteryzować się wysoką odpornością na ścieranie – stąd wybór wyrobów glinokrzemianowych EXTRATON. Dodatkowo, ze względu na konieczność minimalizacji strat ciepła, warstwa izolacyjna oparta na produktach ISOLUX w połączeniu z wełną mineralną gwarantuje doskonałe parametry termoizolacyjne. Kluczowe jest tutaj połączenie właściwości mechanicznych oraz izolacyjnych, aby zapewnić trwałość obmurza przy jednoczesnym utrzymaniu optymalnych parametrów cieplnych pieca.
Strefa wypalania, często utożsamiana ze strefą kalcynacji, jest miejscem, gdzie odbywa się intensywny proces wypału wsadu, takiego jak kamień wapienny lub kamień dolomitowy. Temperatura wypału oraz skład wsadu determinują specyficzne oddziaływanie chemiczne i termiczne, w tym ryzyko hydratacji. W normalnych warunkach roboczych tlenki glinu (Al₂O₃) i krzemu (SiO₂) są chemicznie stabilne, co ogranicza ryzyko reakcji z wodą, jednak konieczne jest zastosowanie materiałów gwarantujących stabilność nawet w kontakcie z wilgocią. W tej strefie kluczowe jest zastosowanie wyrobów, które wykazują wysoką odporność na hydratację oraz stabilność chemiczną przy wysokich temperaturach. Wyroby MULITEX, ANDALUX czy BAUXITEX spełniają te wymagania, gwarantując długotrwałość obmurza przy zmiennych warunkach chemicznych wsadu.
W strefie chłodzenia obmurze jest narażone na stopniowe obniżanie temperatury, co generuje mniej intensywne oddziaływanie termiczne, jednak wymaga odporności na ścieranie. W piecu jednoszybowym na całej wysokości tej strefy zachodzą równomierne procesy chłodzenia, co umożliwia stosowanie jednorodnych rozwiązań izolacyjnych. Dla strefy chłodzenia, najlepiej sprawdzają się materiały szamotowe, które oferują dobrą wytrzymałość na ściskanie oraz odporność na ścieranie. W szczególności zaleca się stosowanie wyrobów gatunku SUPERTON, które są dedykowane dla tej strefy. Dla pieców jednoszybowych, warstwa izolacyjna na całej wysokości wykonana jest z wyrobów ISOLUX oraz uzupełniana wełną mineralną, co zapewnia spójną barierę termiczną i chroni przed stratami ciepła.
W czym pomagamy
Jeżeli chciałbyś uzyskać darmową poradę albo zapytać o dobór wyłożenia ogniotrwałego, zostaw nam swoje dane, a zadzwonimy do Ciebie!
Skontaktuj sięKtóre cegły wysokoglinowe najlepiej opierają się degradacji chemicznej spowodowanej długotrwałą ekspozycją na CO₂ w atmosferze szybu?
Jakie masy do torkretowania lub ubijania oferują optymalną odporność na powtarzające się rozpuszczanie i atak pary z wilgotnego wsadu wapna?
Jak należy zoptymalizować kształt cegieł, konstrukcję kotew stalowych i konfigurację spoin dla wysokiej geometrii szybu, aby uwzględnić osiową rozszerzalność cieplną i zapobiec zawaleniu się wyłożenia?
Piec Maerz’a
Piec Maerz'a, stosowany w procesach wymagających precyzyjnej kontroli temperatury i równomiernego rozkładu ciepła, charakteryzuje się warunkami pracy w których ceramiczne obmurza ogniotrwałe są narażone na bardzo wysokie temperatury, często przekraczające 1200°C. W piecach Maerz'a szczególną rolę odgrywa zasada rewersji, która jest kluczowym elementem różnicującym je na tle innych pieców szybowych. W piecach Maerz'a wykorzystywane są dwa szyby: w jednym odbywa się proces kalcynacji kamienia wapiennego, a drugi pełni funkcję dostarczania powietrza. Zasada rewersji polega na tym, że procesy w piecu są realizowane na przemian w odwrotnej kolejności — najpierw spalanie, a potem kalcynacja. Dzięki temu możliwa jest bardziej efektywna kontrola temperatury oraz poprawa wykorzystania energii, ponieważ procesy odbywają się naprzemiennie, co pozwala na lepsze zarządzanie obiegiem gazów. Dzięki wyższej wydajności oraz trudniejszym warunkom pracy w piecach Maerz'a, konieczne jest zastosowanie materiałów ogniotrwałych o wyższej jakości niż w piecach szybowych. Materiały te muszą wykazywać wysoką odporność na szok termiczny oraz erozję chemiczną, aby zachować integralność obmurza w zmieniających się warunkach. Optymalizacja dystrybucji ciepła oraz minimalizacja strat termicznych są kluczowe w zapewnieniu efektywności technologii oraz długotrwałej eksploatacji urządzenia.
Zakres: Projektowanie Produkcja Montaż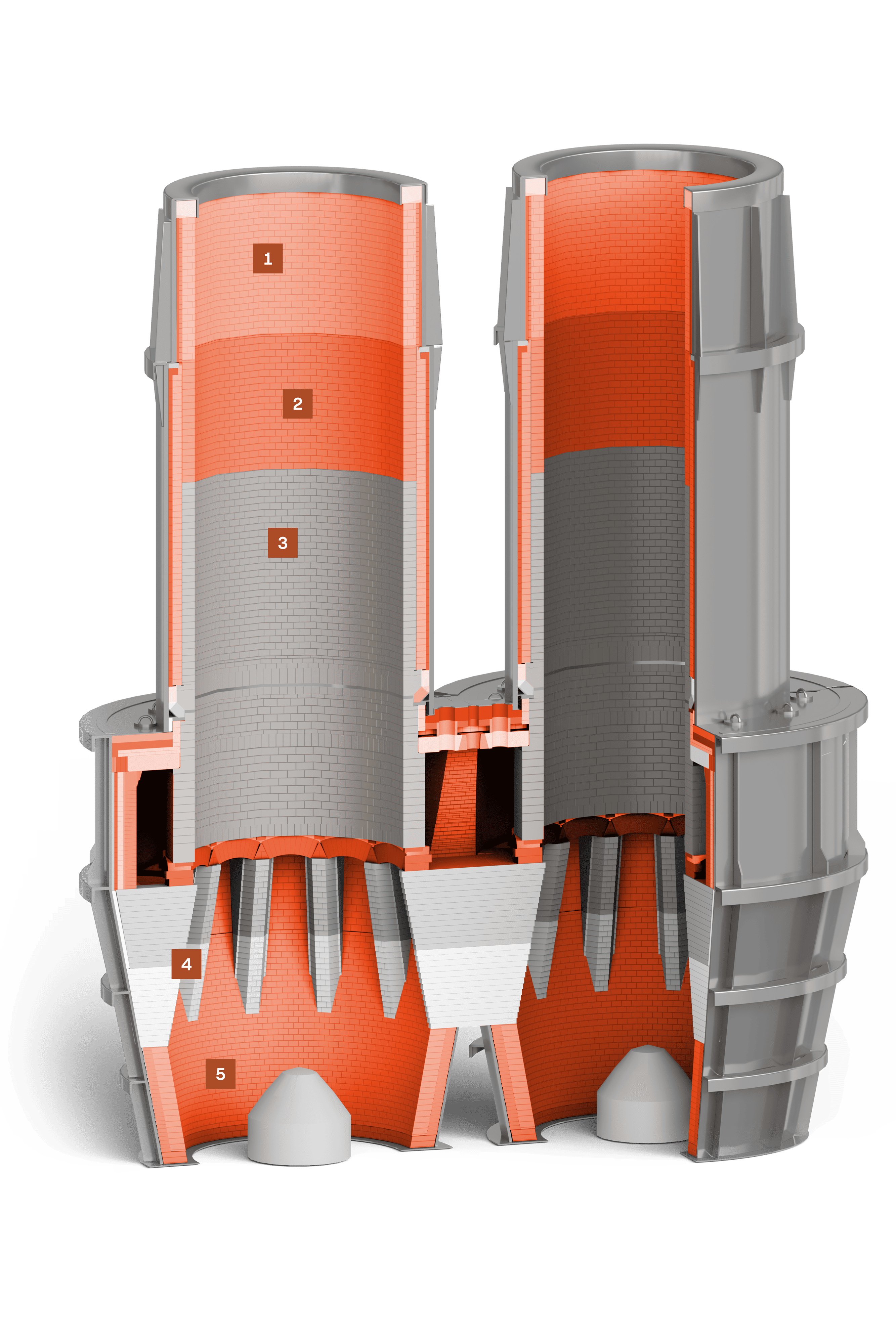
Strefa podgrzewania w piecu Maerza rozciąga się od dolnego poziomu palników do górnej części szybu, gdzie cyklicznie załadowywany jest kamień wapienny zmieszany z paliwem. Proces ten generuje intensywne oddziaływanie ścierające oraz termiczne, wynikające z bezpośredniego kontaktu wsadu z wyłożeniem oraz zmiennych warunków temperaturowych. Dlatego w tej strefie kluczowe jest zapewnienie materiałom wysokiej odporności na ścieranie oraz minimalizacja strat ciepła, co przekłada się na efektywność całego pieca. Konstrukcja obmurza w strefie podgrzewania opiera się na zastosowaniu różnych materiałów, które są dobierane w zależności od warunków temperaturowych. W dolnej części, w okolicy palników, warstwa robocza wykonana jest z wyrobów magnezytowo-spinelowych, które cechują się wysoką odpornością na ścieranie i działanie agresywnych substancji powstających podczas spalania. Natomiast w górnej części szybu stosowane są wyroby glinokrzemianowe o podwyższonej odporności na ścieranie, reprezentowane przez produkty z linii EXTRATON.
Aby zapewnić płynne przejście między warstwą magnezytowo-spinelową a glinokrzemianową, wprowadza się warstwę przejściową wykonaną z wyrobów wysokoglinowych (andaluzytowych). Dodatkowo, przestrzeń pomiędzy pancerzem a warstwą roboczą wyłożona jest systemem izolacyjnym, który obejmuje płyty izolacyjne dostępne w ofercie ISOLUX oraz maty izolacyjne wykonane z wełny mineralnej. W niektórych rozwiązaniach stosuje się także dodatkową warstwę izolacyjną wykonaną z wyrobów SUPERTON lub EXTRATON, umieszczoną pomiędzy warstwą roboczą a głównym systemem izolacyjnym. Całość wymurówki szybu kończy warstwa betonu konwencjonalnego, stanowiąca finalne wykończenie i zabezpieczenie konstrukcji.
Strefa wypału rozciąga się od dolnego poziomu sklepień nośnych do dolnego poziomu palników (lanc gazowych). W tej części pieca wsadu poddawany jest intensywnemu procesowi wypału, który generuje zarówno bardzo wysokie temperatury, jak i silne oddziaływania chemiczne, zależne od rodzaju używanego wsadu – na przykład kamienia wapiennego lub dolomitowego. PCO Żarów dostarcza wyroby warstw ochronnej i izolacyjnej strefy wypału. Całość wyłożenia szybu, począwszy od strefy dylatacji w górę, opiera się na zastosowaniu specjalnych kształtek, takich jak typy AS1, AS2 i podobne, wykonanych z materiałów MULITEX lub ANDALUX. Takie rozwiązanie gwarantuje nie tylko stabilność konstrukcyjną, ale również odporność na zmienne warunki wypału.
W konstrukcji pieca Maerz’a wyróżnia się elementy takie jak filary, sklepienia między filarowe, sklepienia płaskie oraz kanał łączący, które wykonuje się z betonów niskocementowych lub bezcementowych. Wykonanie filarów w piecu Maerza wymaga zastosowania kombinacji tzw. Kształtek dziobowych (VK-76x i WL-76) które gwarantują wyjątkową stabilność konstrukcji. W przypadku pieca Maerza bezfilarowego, stopa cylindra podwieszonego również wykonana jest z wytrzymałych betonów, a na sklepieniu płaskim stosuje się warstwę izolacyjną wykonaną z lekkich betonów izolacyjnych typu ISOCAST lub ISOGUN, uzupełnionych o wełnę mineralną.
Strefa chłodzenia w piecu Maerza rozciąga się od poziomu pierwszej warstwy wyłożenia do dolnego poziomu sklepień międzyfilarowych. W tej części urządzenia następuje stopniowe obniżanie temperatury, co jest kluczowe dla stabilizacji procesu chłodzenia. Mimo spadku temperatur, wyłożenie pozostaje narażone na intensywne oddziaływanie ścierające i mechaniczne, wynikające zarówno z ruchu wsadu, jak i z naprężeń generowanych podczas procesu chłodzenia. Warstwa robocza jest wykonana z wyrobów szamotowych, gatunków SUPERTON lub EXTRATON, które doskonale sprawdzają się w tych warunkach. Przestrzeń międzyfilarowa jest najczęściej murowana z wyrobów EXTRATON Warstwa izolacyjna w strefie chłodzenia opiera się na wyrobach ISOLUX, które stosuje się w połączeniu z płytami CaSi oraz matami wykonanymi z wełny mineralnej.
W czym pomagamy
Jeżeli chciałbyś uzyskać darmową poradę albo zapytać o dobór wyłożenia ogniotrwałego, zostaw nam swoje dane, a zadzwonimy do Ciebie!
Skontaktuj sięJaki design kształtek filarowych pieca może wpłynąć na zwiększenie odporności mechanicznej wyłożenia?
Które materiały ogniotrwałe najlepiej sprawdzą się w warunkach równoległej ekspozycji na ścieranie i atak chemiczny podczas procesu kalcynacji kamienia wapiennego?
Jak zaprojektować warstwy przejściowe i ochronne pomiędzy wyrobami zasadowymi i glinokrzemianowymi aby uwzględnić rozszerzalność przy nagrzewaniu i chłodzeniu wyłożenia?
Piec obrotowy wapienniczy do produkcji pulpy
Piec obrotowy wapienniczy prowadzi proces odzysku wapna (proces Krafta) z pulpy wapiennej, aby następnie użyć go w procesie produkcji celulozy. Wymurówka pieca obrotowego jest przeważnie dwuwarstwowa, co zapewnia odpowiednią trwałość i odporność na ekstremalne warunki pracy. Dla wymurówki ogniotrwałej największymi zagrożeniami są: szybkie zmiany temperatury, reakcja cegieł z wapienną szlamą, zmiany ciśnienia i naprężenia spowodowane obrotami pieca. W piecach obrotowych wapienniczych stosuje się różne materiały ogniotrwałe w zależności od strefy. Na wlot i wylot pieca stosuje się betony ogniotrwałe o wysokiej odporności na szok termiczny i chemiczny, a także cegły szamotowe i andaluzytowe. W strefie wypału najczęściej stosuje się cegły andaluzytowe z dodatkiem P2O5, które gwarantują odporność na ekstremalne temperatury, agresywne substancje chemiczne oraz zapewniają wysoką wytrzymałość mechaniczną.
Zakres: Projektowanie Produkcja Montaż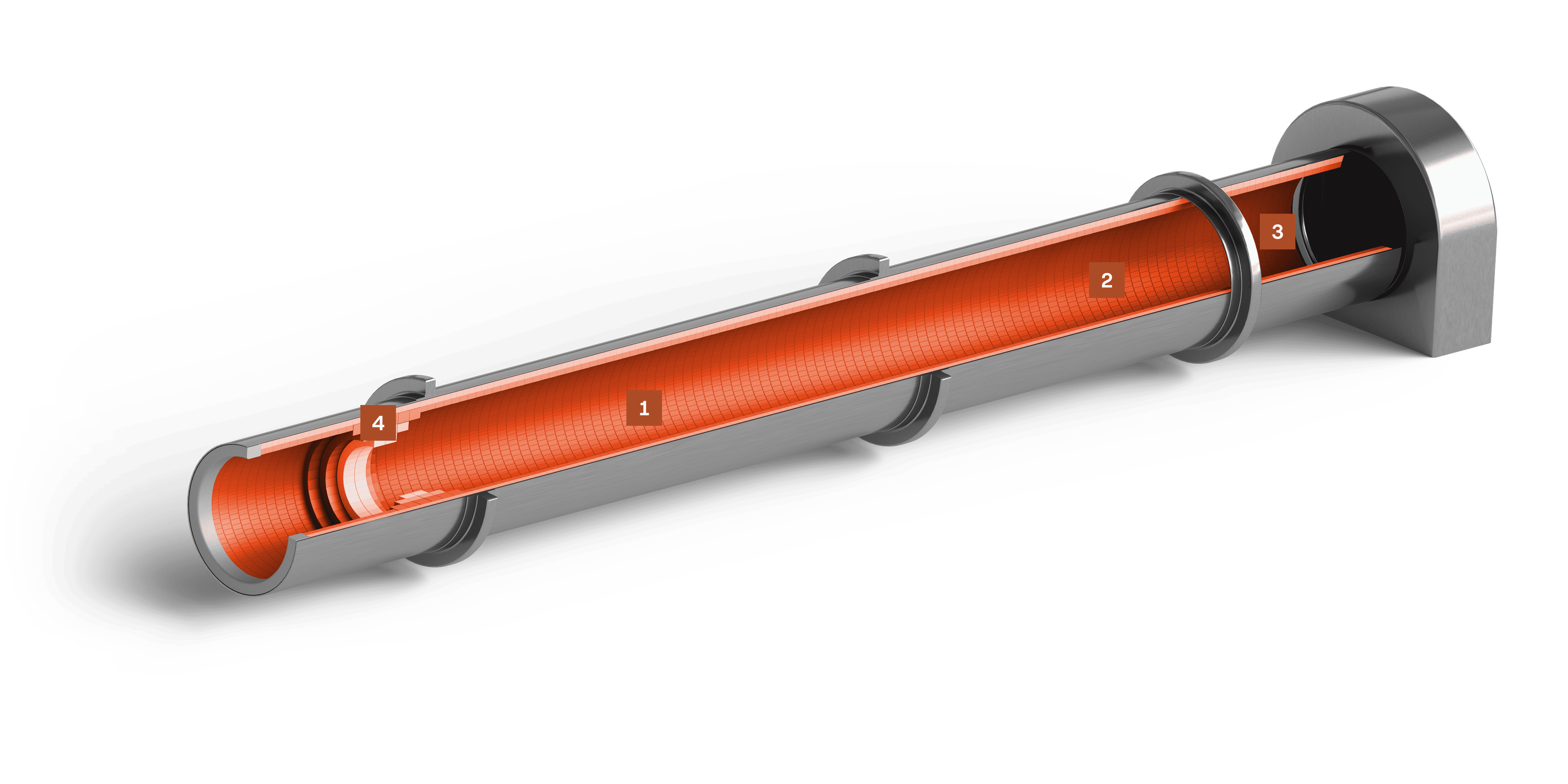
Strefa podgrzewania pieca obrotowego wapienniczego to obszar przyrostu temperatury od 200 °C do 1100 °C . W tym miejscu pulpa jest suszona i wstępnie kalcynowana. Obmurze ogniotrwałe doświadcza ścierania i erozji chemicznej. Pulpa zawiera domieszki soli alkaicznych, siarki, chlorków – to stwarza ryzyko infiltracji chemicznej wyłożenia. Czynnikiem ryzyka jest też to, że pulpa jest wilgotna (do 20% wilgotności) i obmurze musi być odporne na wsiąkanie wody w pory. Dla warstwy roboczej polecane jest stosowanie wysokiej klasy wyrobów szamotowych o niskiej porowatości i odpornych na alkalia – EXTRATON. W części bliżej strefy wypału temperatury są na tyle wysokie, że należy rozważyć wyroby wysokoglinowe lub chemicznie wiązane – ANDALUX.
Zakres temperatur w tej strefie to 1100 °C do 1300 °C na całej długości. Panują tu zmienne warunki pracy; czynnikiem ryzyka są głównie naprężenia termiczne (pochodzące z płomienia palnika) oraz chemiczne, skutek oddziaływania gazów. Pulpa wapienna jest spiekana, ulega przemianie z błota wapiennego zawierającego węglany do czystego CaO (wapna palonego). Obmurze ogniotrwałe musi być odporne na szok termiczny, wysoką temperaturę oraz korozję chemiczną i mechaniczną. Wyłożenie jest dwuwarstwowe, dla warstwy roboczej tej strefy polecane są cegły andaluzytowe chemicznie wiązane klasy ANDALUX.
Jest to najkrótszy odcinek pieca obrotowego i obejmuje kilka metrów przed wlotem do chłodnika. Następuje tam szybki spadek temperatury, z 1000 °C do około 200 °C . To powoduje znaczne szoki termiczne. W tej strefie produktem jest już przereagowane wapno, które działa na wymurówkę ściernie (przesuwanie wsadu). Ruch rotacyjny pieca i konstrukcja zwężająca (zmniejszenie średnicy pieca) skutkuje naprężeniem mechanicznym niebezpiecznym dla wyłożenia ogniotrwałego. Wyłożenie jest dwuwarstwowe; na przewężeniach stosuje się w warstwie roboczej beton ogniotrwały wysokoglinowy a w warstwie izolacyjnej – płytki formowane ISOLUX o podwyższonej odporności na ściskanie.
Próg spiętrzający wykonany jest z ceramiki ogniotrwałej i ma za zadanie wyrównać dystrybucję wsadu na wylocie pieca obrotowego. W tej strefie występuje znaczne ścieranie wymurówki i naprężenie mechaniczne. Zalecana zabudowa obejmuje najbardziej wytrzymałe cegły andaluzytowe, które zapewniają regulację procesu przesuwania wsadu.
W czym pomagamy
Jeżeli chciałbyś uzyskać darmową poradę albo zapytać o dobór wyłożenia ogniotrwałego, zostaw nam swoje dane, a zadzwonimy do Ciebie!
Skontaktuj sięKtóry materiał sprawdzi się jako wyłożenie robocze w kontakcie ze smołą i kwasami pochodzenia organicznego?
Jak można zabezpieczyć wykładzinę przed pęknięciami z powodu różnic rozszerzalności pancerza, warstwy izolacyjnej i warstwy roboczej?
Jak wykryć nadmierne zużycie wymurówki ogniotrwałej w miejscach zbierania się osadów i w rejonie palnika?
Dlaczego PCO
Zabudowa w pakiecie z dostawami ceramiki – łatwiejsze zarządzanie projektem i jeden gwarant jakości
Kompletna oferta wyrobów glinokrzemianowych dla branż produkcji cementu i wapna
Posiadamy własny zespół konstruktorów i projektantów gotowych pomóc z każdym wyzwaniem
Wybrane produkty i usługi
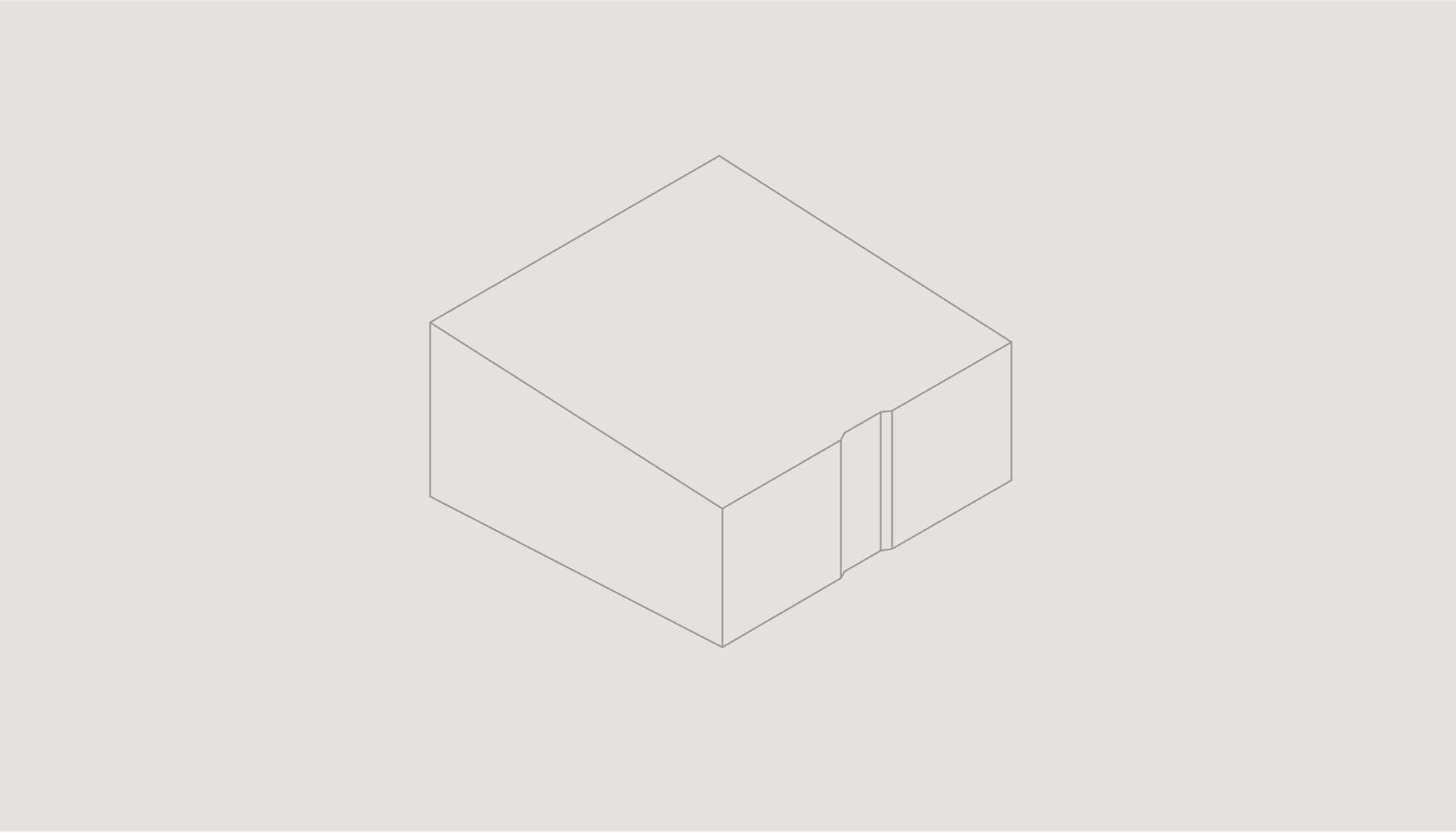
Linia produktów ABRAL
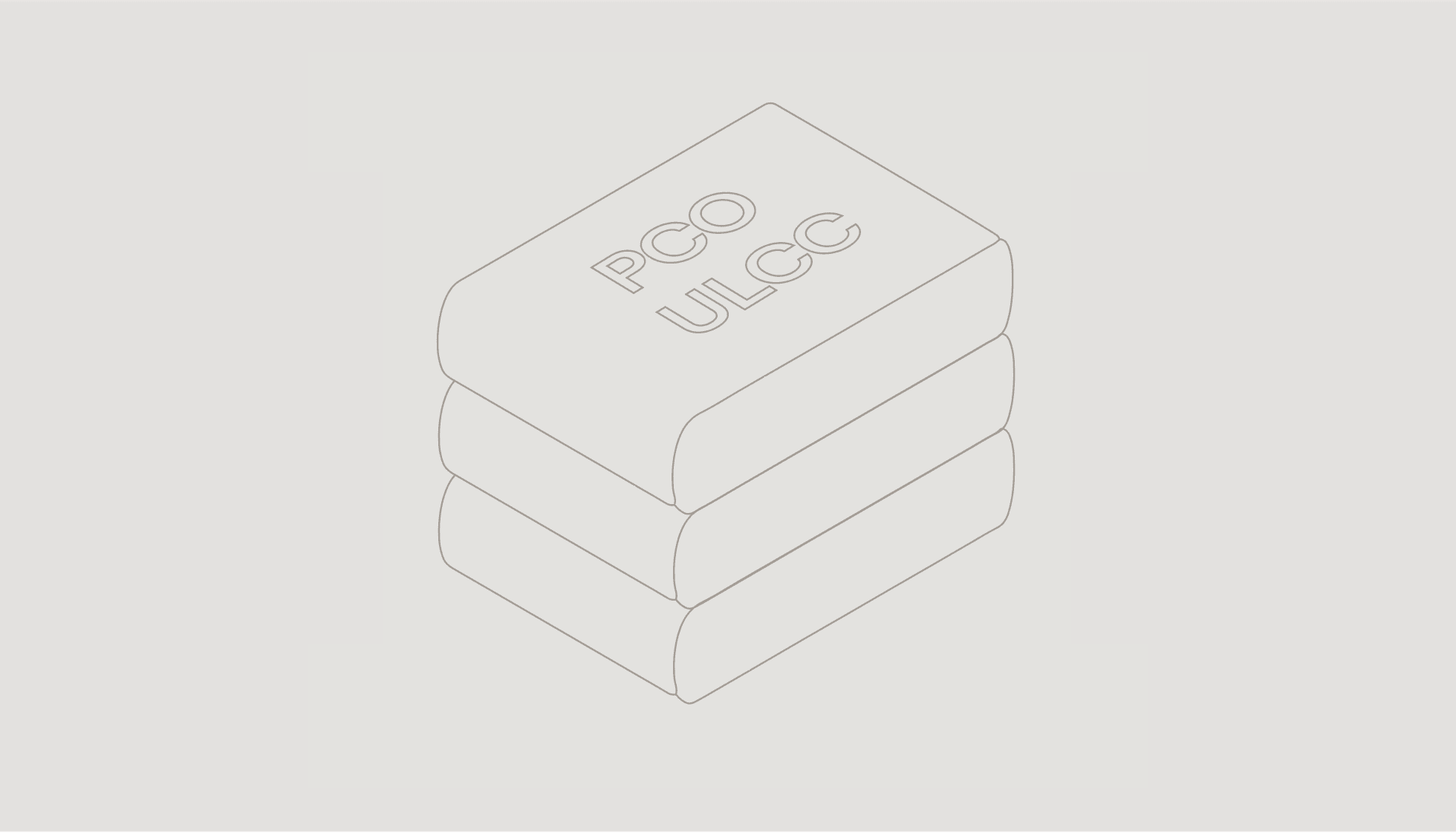
Betony ogniotrwałe ultra-niskocementowe (ULCC)
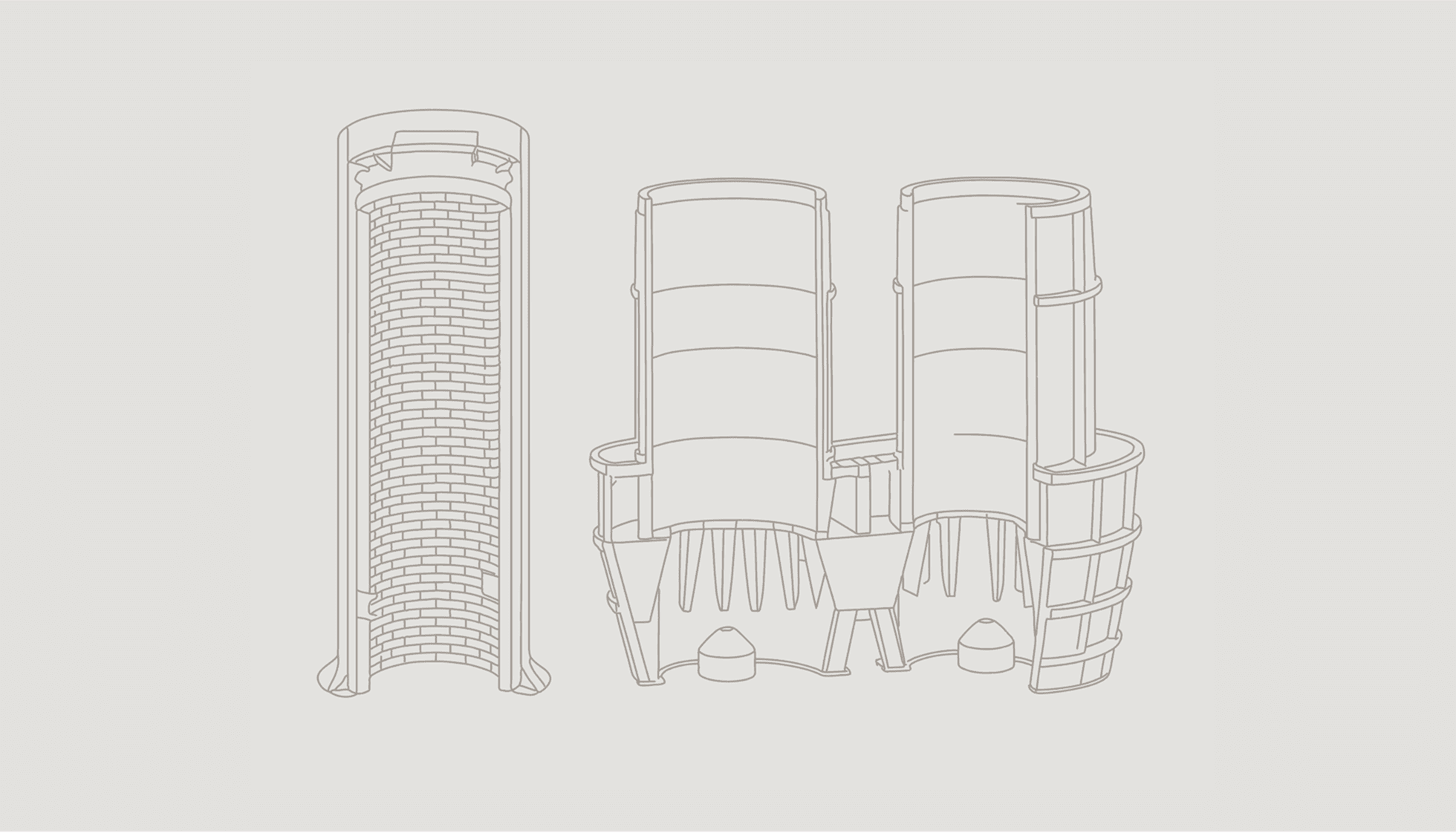
Nadzór nad zabudową pieców szybowych i pieców Maerza
Skontaktuj się
Wybierz pozycję która najlepiej opisuje temat, na który chcesz z nami porozmawiać. To pozwoli nam skierować Twoje zapytanie do odpowiedniej osoby w PCO.